What factors affect the grinding efficiency and wear resistance of high chrome casting cylpebs?
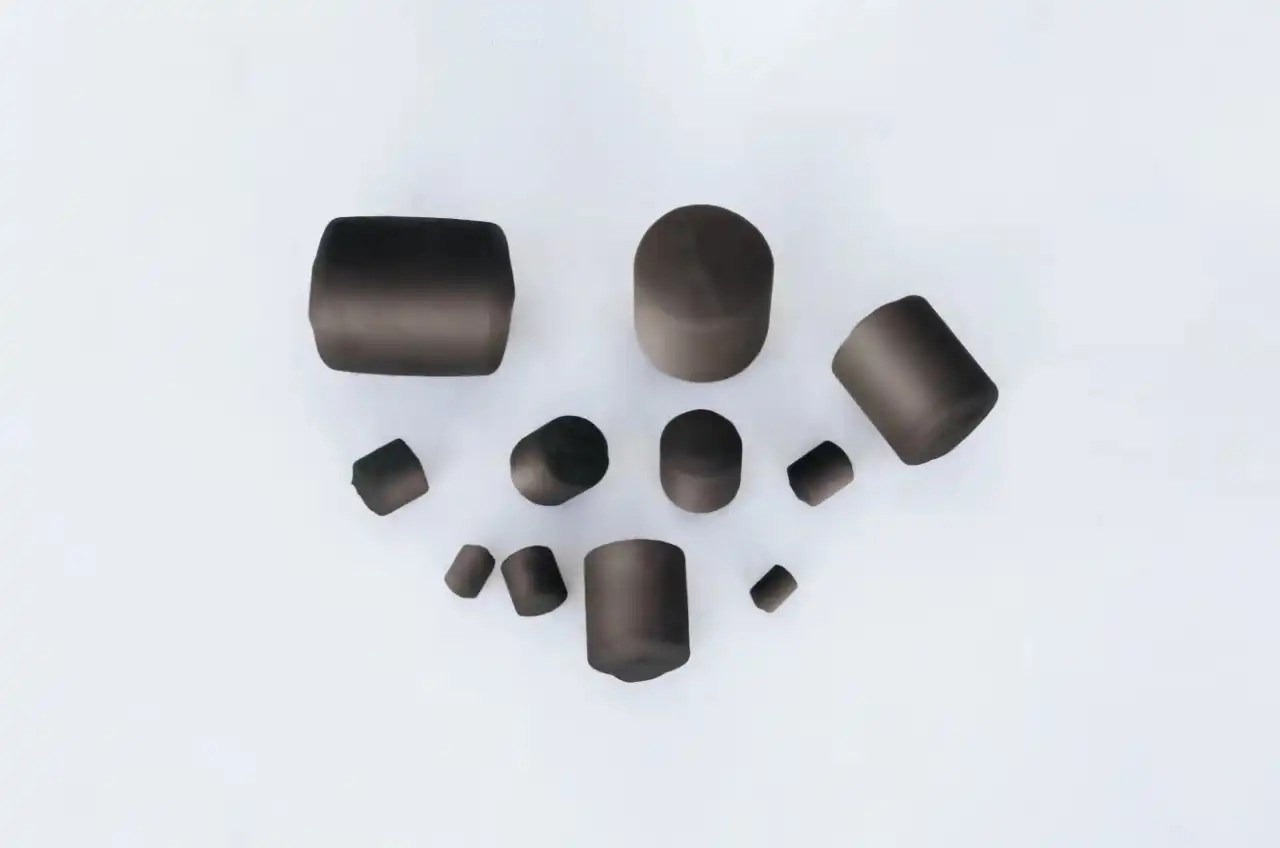
In the realm of industrial grinding, the efficiency and wear resistance of high chrome casting cylpebs play a pivotal role in the overall performance of grinding mills. As someone deeply involved in the field, I've delved into understanding the multifaceted factors influencing these crucial components. In this article, I'll explore the key aspects affecting grinding efficiency and wear resistance, while also shedding light on the utilization and calculation methodologies pertinent to high chrome grinding media.
Exploring Different Materials Used in Grinding Balls
What Makes Grinding Cylpebs a Sustainable Choice?

grinding cylpebs have emerged as a sustainable choice due to their unique combination of durability, efficiency, and environmental friendliness. Durability: The products are designed to withstand the harsh conditions of grinding operations, ensuring a longer lifespan compared to other grinding media. Their robust construction reduces the need for frequent replacements, minimizing waste and conserving resources. Efficiency: The products are highly efficient in their grinding performance, leading to lower energy consumption during grinding operations. This reduced energy usage contributes to a more sustainable manufacturing process and minimizes greenhouse gas emissions. Eco-friendly nature: The products are often manufactured using recycled materials, such as scrap metal, which helps conserve natural resources and reduce waste. Additionally, their durable design extends their lifespan, further reducing the environmental impact associated with waste generation.
How Do Different Materials Affect Grinding Ball Performance?
how to make aluminum powder without a ball mill?
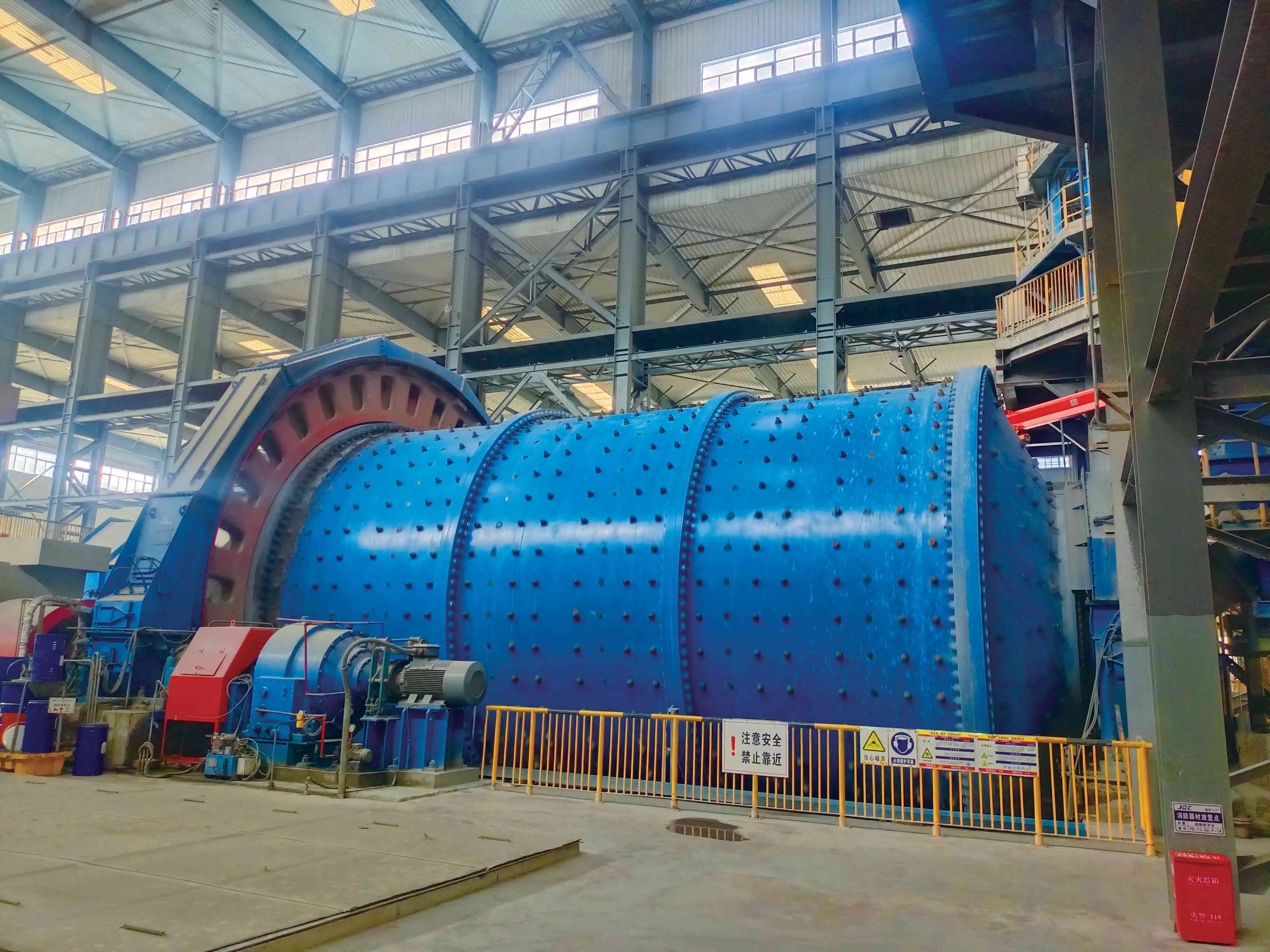
Using Ball Mill Balls factory to make aluminum powder at home can be an interesting and rewarding project. Making aluminum powder doesn't necessarily need costly hardware, so you can involve it for fireworks, metallurgical examination, or similarly as a side interest. In this blog, we'll look at different ways to make aluminum powder without a ball plant, answer some frequently asked questions about ball factory balls, and give a detailed guide for home enthusiasts.
How do you determine the quality of grinding balls?
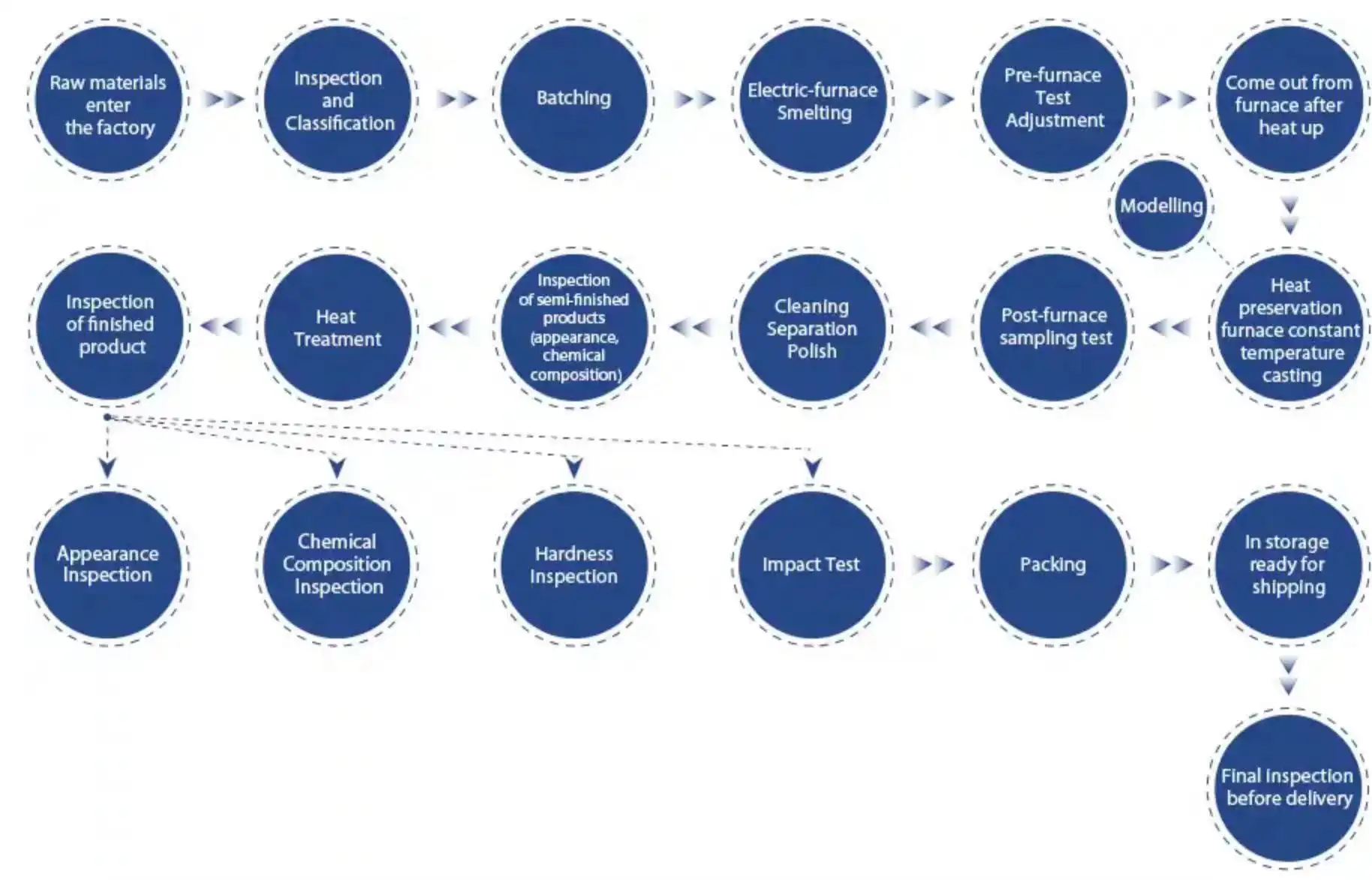
Grinding balls are essential in various industrial applications, particularly in mining, cement manufacturing, and thermal power generation. Determining the quality of grinding balls is crucial for ensuring efficient and effective grinding processes. High-quality grinding balls can significantly impact the performance and longevity of milling operations.
How do ball mill grinding media affect the milling efficiency?
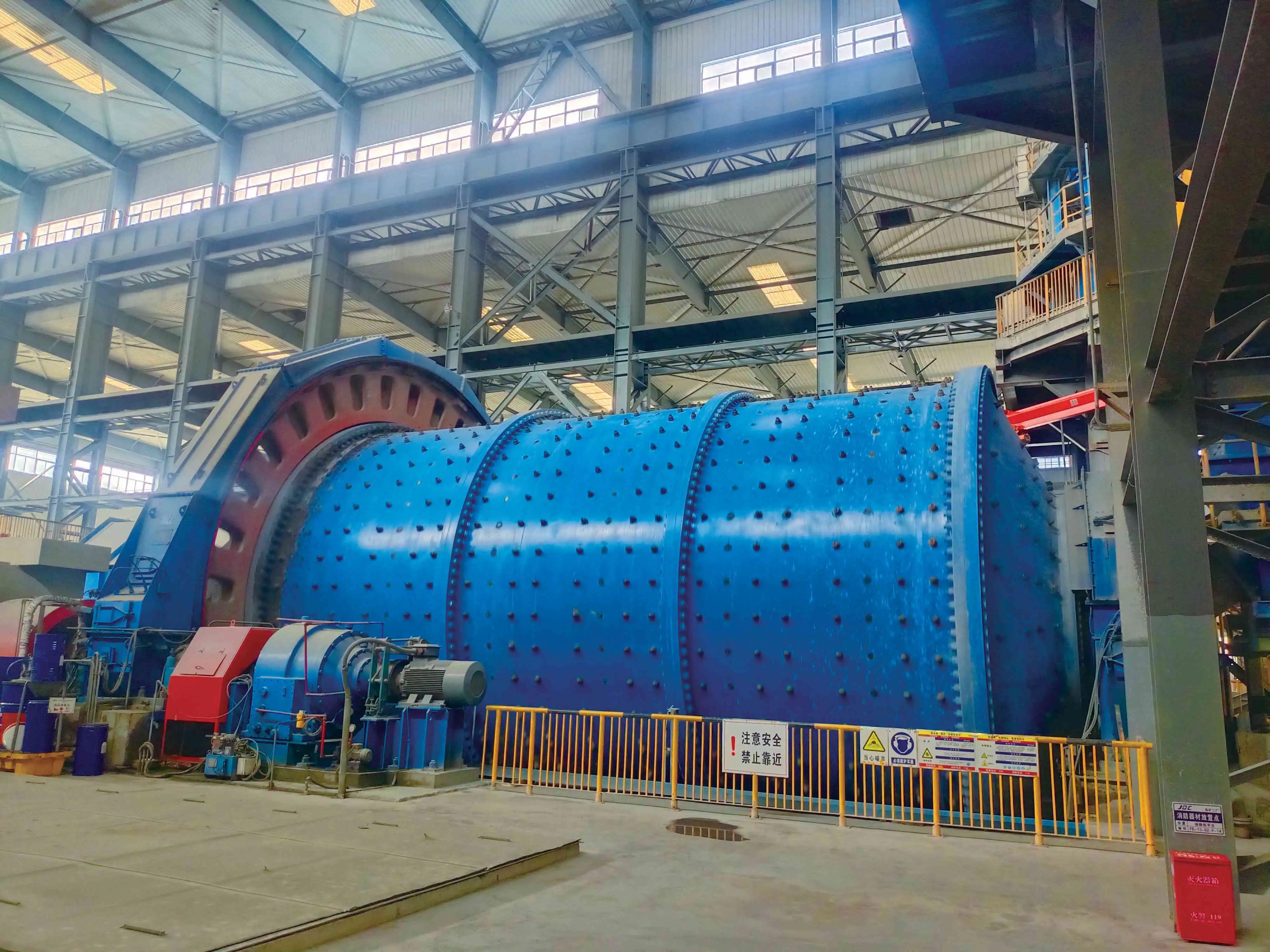
Ball mill grinding media are crucial for milling efficiency, affecting particle size reduction. Their size, shape, material composition, and wear resistance significantly impact grinding performance. High-quality media improve efficiency, reduce energy consumption, and extend equipment lifespan. Proper selection optimizes the milling process, influencing particle size distribution, grinding time, and product quality. Factors like hardness, density, and surface properties enhance grinding effectiveness. By choosing and maintaining the right media, industries can achieve better milling results, increase productivity, and lower operational costs.
What are the common applications of grinding balls in the mining sector?
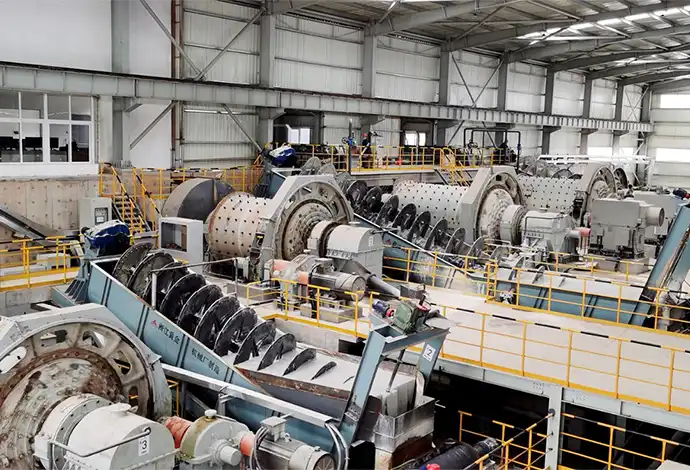
Grinding Balls for Mining are essential in the mining sector, used for ore comminution, mineral liberation, and particle size reduction in ball mills. They help break down hard rock materials, such as gold, copper, and iron ores, into finer particles, enhancing the surface area for more efficient processing and mineral recovery. Grinding balls are also key in preparing mineral concentrates, aiding in separating valuable minerals from gangue materials. Their versatility spans from primary crushing to fine grinding, significantly boosting the efficiency and productivity of mineral extraction operations.
Essential Tips for Using Cement Grinding Media Balls
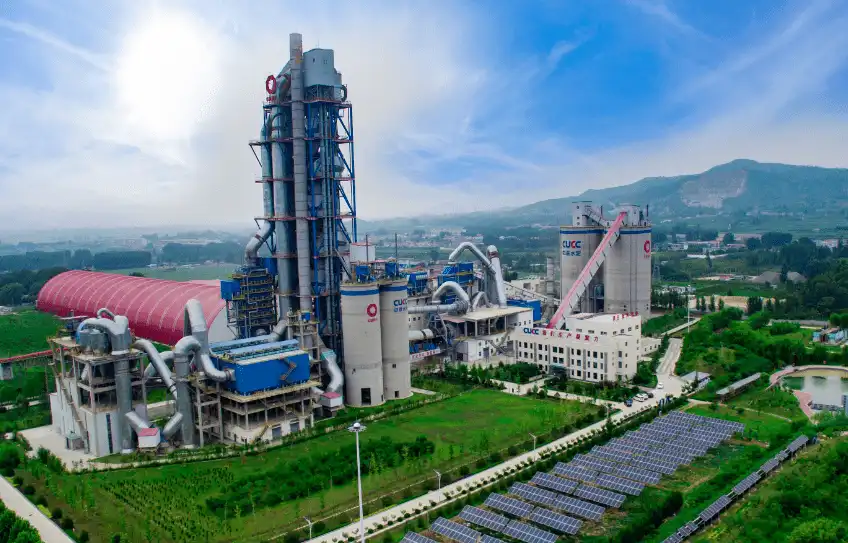
In the cement industry, grinding media balls play a crucial role in the production process. These cement grinding media balls are essential components in ball mills, where they crush and grind raw materials into fine particles. To ensure optimal performance and longevity of your grinding media, it's important to follow best practices for their use and maintenance. In this article, we'll explore key tips for effectively using cement grinding media balls, including maintenance strategies, wear reduction techniques, and cost optimization methods.
Innovative Applications of High Chrome Grinding Media in Industries
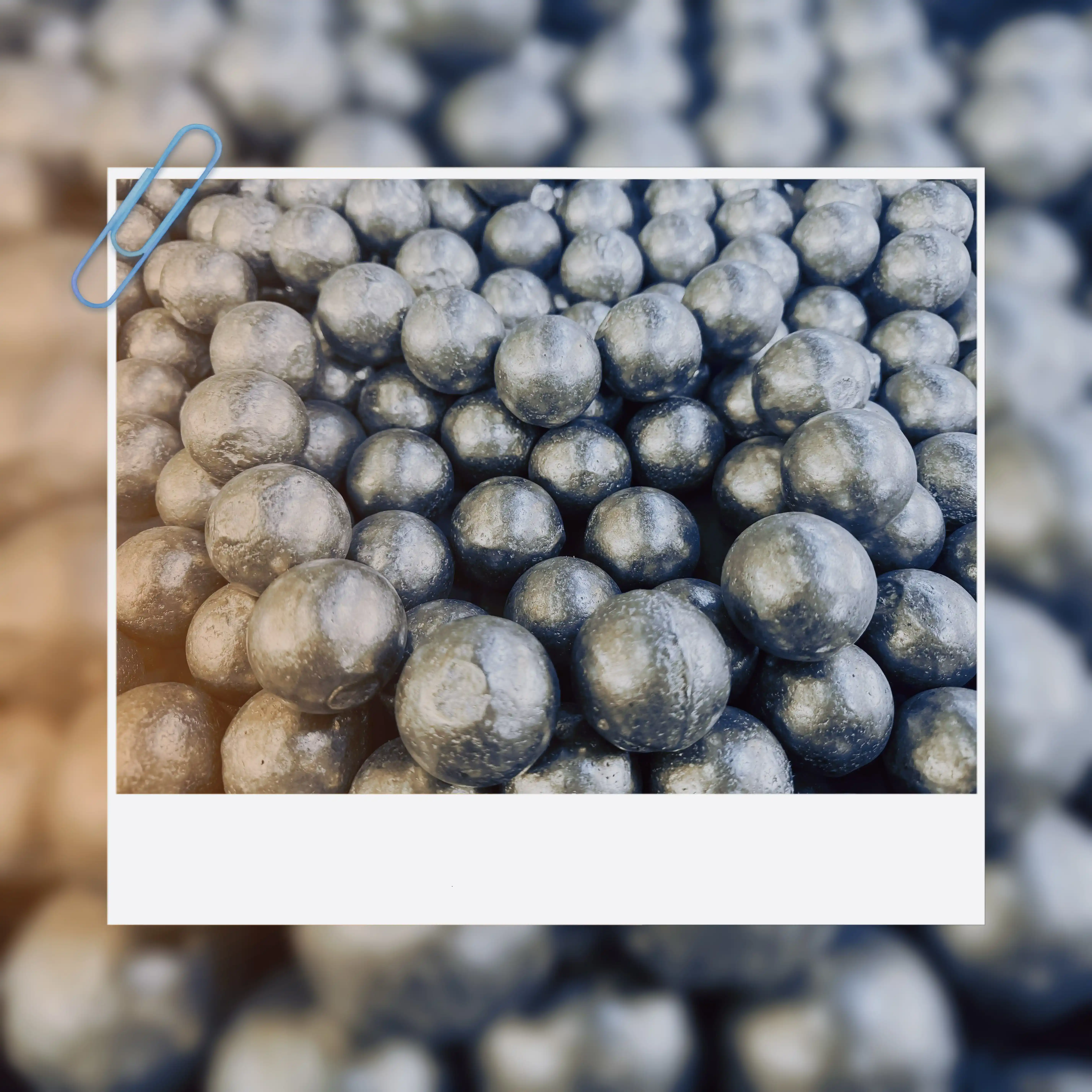
The world of industrial manufacturing and processing is constantly evolving, with new technologies and materials emerging to enhance efficiency and productivity. Among these innovations, high chrome grinding media has emerged as a game-changer in various sectors. This blog post explores the cutting-edge applications of chrome grinding media across different industries, showcasing how this versatile material is revolutionizing production processes and improving output quality.
How does media density influence grinding efficiency?
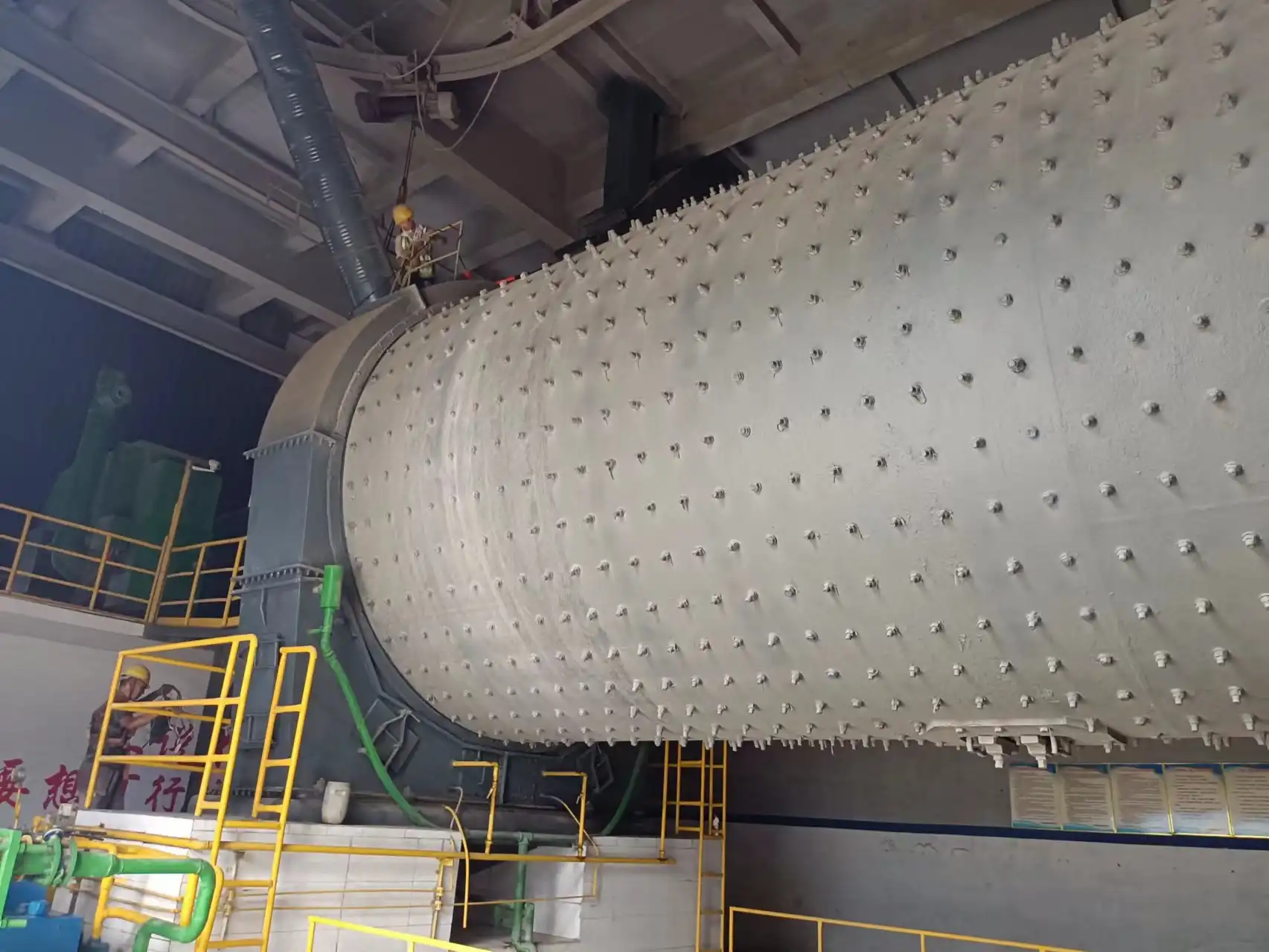
In the world of industrial grinding, the efficiency of the process is paramount. One crucial factor that significantly impacts grinding efficiency is the density of the grinding media used in ball mills. At NINGHU, we specialize in manufacturing high-quality grinding media, including high and low chrome casting grinding balls and cylpebs. Our extensive experience in wear-resistant materials production allows us to offer insights into how ball mill media density affects grinding efficiency. Let's delve into this topic and explore the intricacies of media density's influence on the grinding process.
How to Select the Right Cylpebs Grinding Media for Your Grinding Application?
.webp)
Selecting the appropriate cylpebs grinding media is an essential step in optimizing the efficiency and cost-effectiveness of your grinding process. Whether you're operating in the mining, cement, or chemical industry, the choice of grinding media can have a profound impact on your production output, energy consumption, and overall operational performance. Cylpebs, with their unique shape and properties, provide several advantages over traditional grinding balls, including increased surface area for grinding, better packing density, and enhanced grinding efficiency. Understanding the specific requirements of your grinding operation—such as material characteristics, throughput needs, and desired particle size—will help guide you in selecting the most suitable cylpebs. This guide aims to assist you in making an informed decision based on your unique grinding needs, ensuring that you achieve the best possible results and maximize operational efficiency.