How do you calculate grinding media in a ball mill?
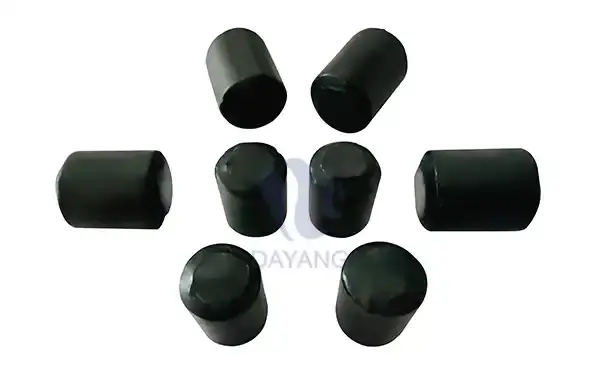
The determination of the quantity of grinding media that is required in a ball mill is an essential step in ensuring the effectiveness of the milling process. Grinding media like ceramic balls, flint pebbles, and stainless steel balls are needed to break down the material in the mill. The efficiency and nature of the processing process are directly influenced by the type and quantity of grinding cylpebs used.
How Can Grinding Balls Reduce Grinding Media Consumption?
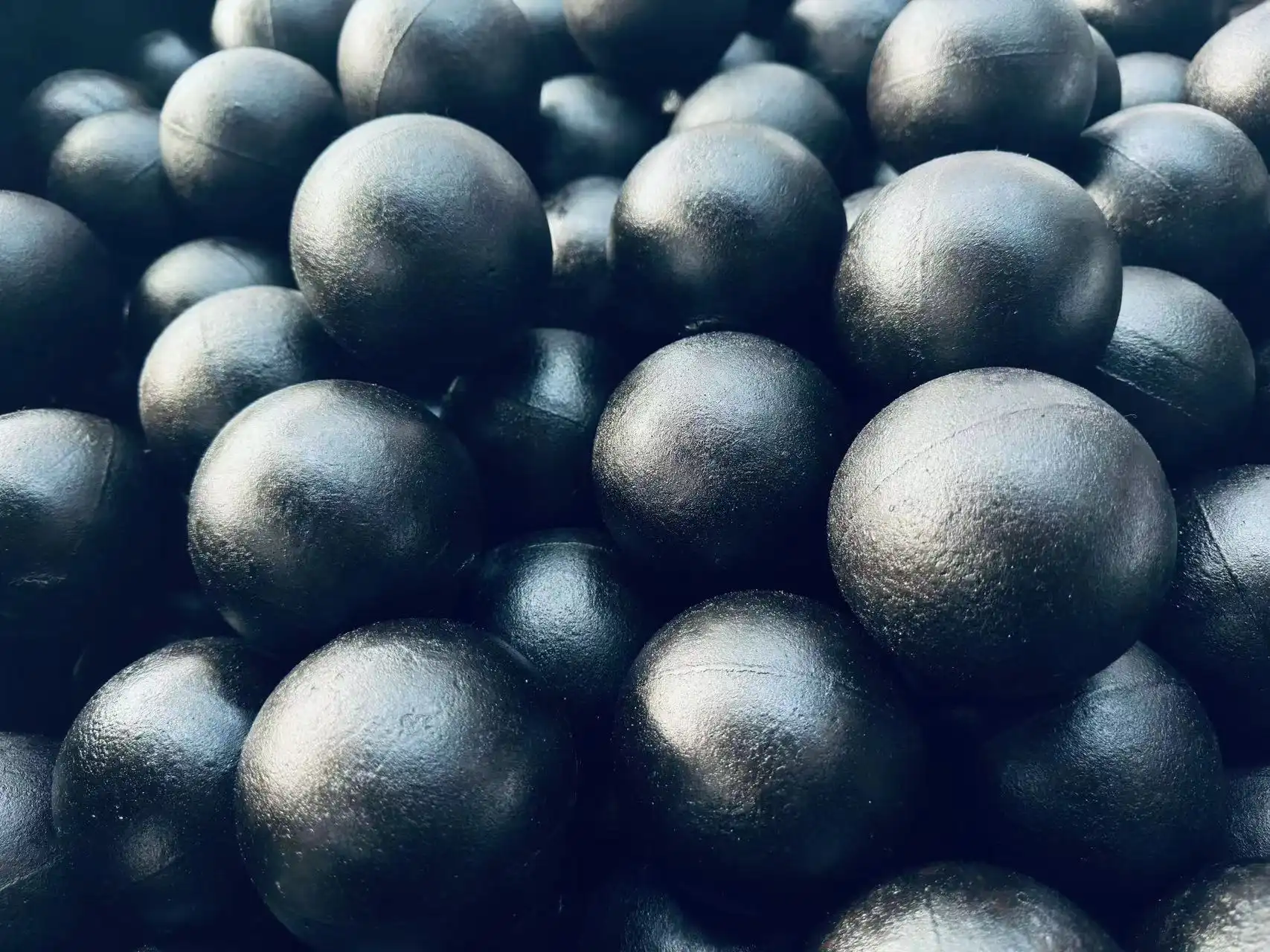
In industries like cement production, mining, and power generation, grinding media is an essential component of the milling process. However, the cost of grinding media can be substantial, especially when considering the large volumes required. Reducing grinding media consumption is not just about cutting costs; it's also about improving efficiency, prolonging equipment life, and minimizing environmental impact. But how can grinding balls contribute to this goal? In this article, we'll explore how the right choice of grinding balls can help reduce grinding media consumption while maintaining or even enhancing operational efficiency.
What is the Hardness of Grinding Balls?
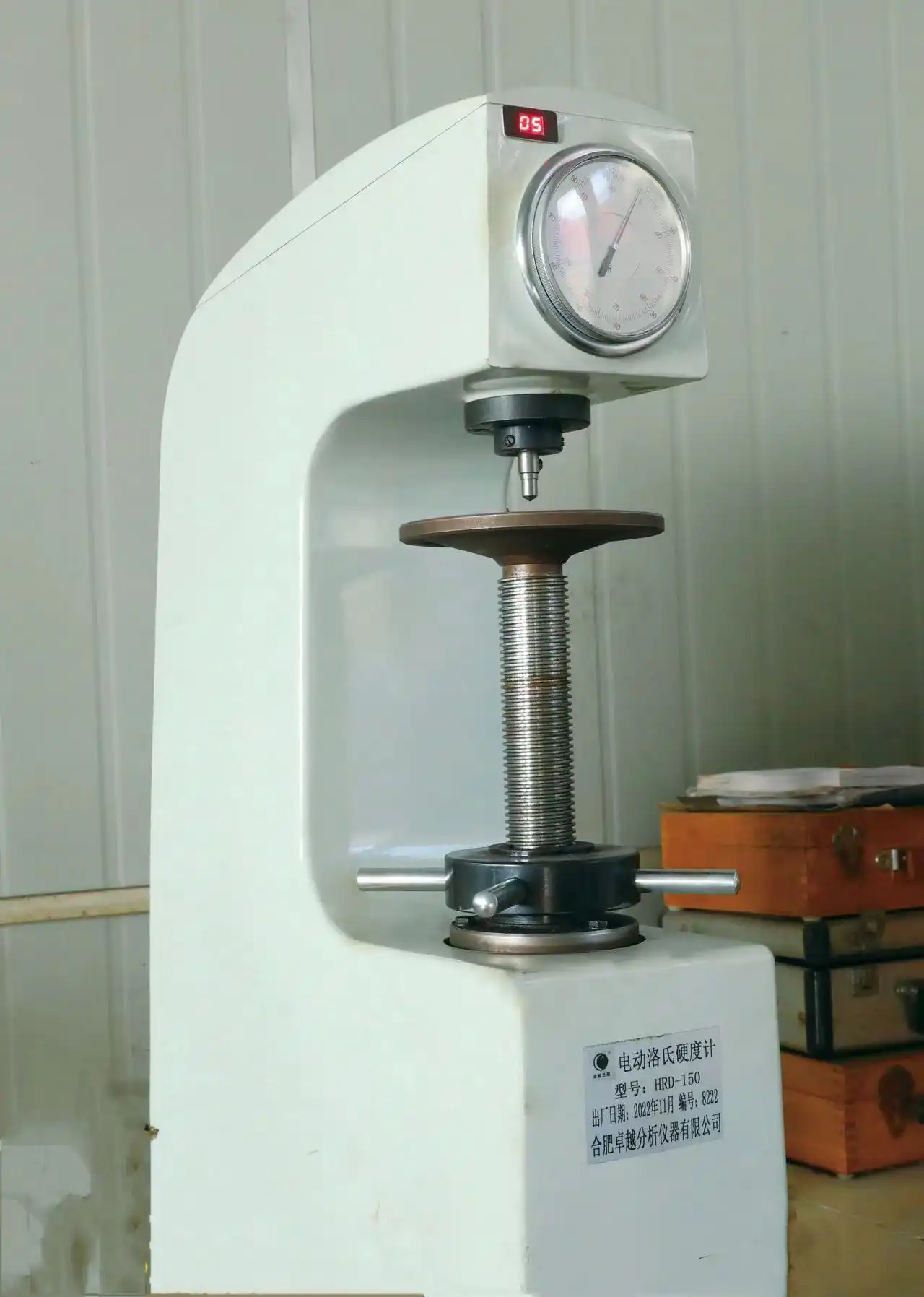
Grinding Ball are a necessary part of a lot of industrial processes, especially mining and ore processing, where they are used to extract valuable minerals from ore. The effectiveness and longevity of grinding balls are directly impacted by their hardness, so knowing their hardness is essential. Hardness impacts how well the balls wear out materials and oppose misshapening under pressure, eventually influencing the effectiveness of the whole processing process.
Can grinding balls be used for both wet and dry milling?
Grinding balls are essential components in ball milling operations, crucial for pulverizing materials into fine particles in both wet and dry conditions. Understanding their versatility is key to optimizing milling processes for various applications. Grinding balls play a vital role in the process of ball milling, which is widely used in various industries for the production of powders and materials. Whether in wet or dry milling applications, these spheres are capable of effectively reducing the size of particles, enhancing mixing processes, and facilitating chemical reactions.
How are high chrome grinding balls produced?
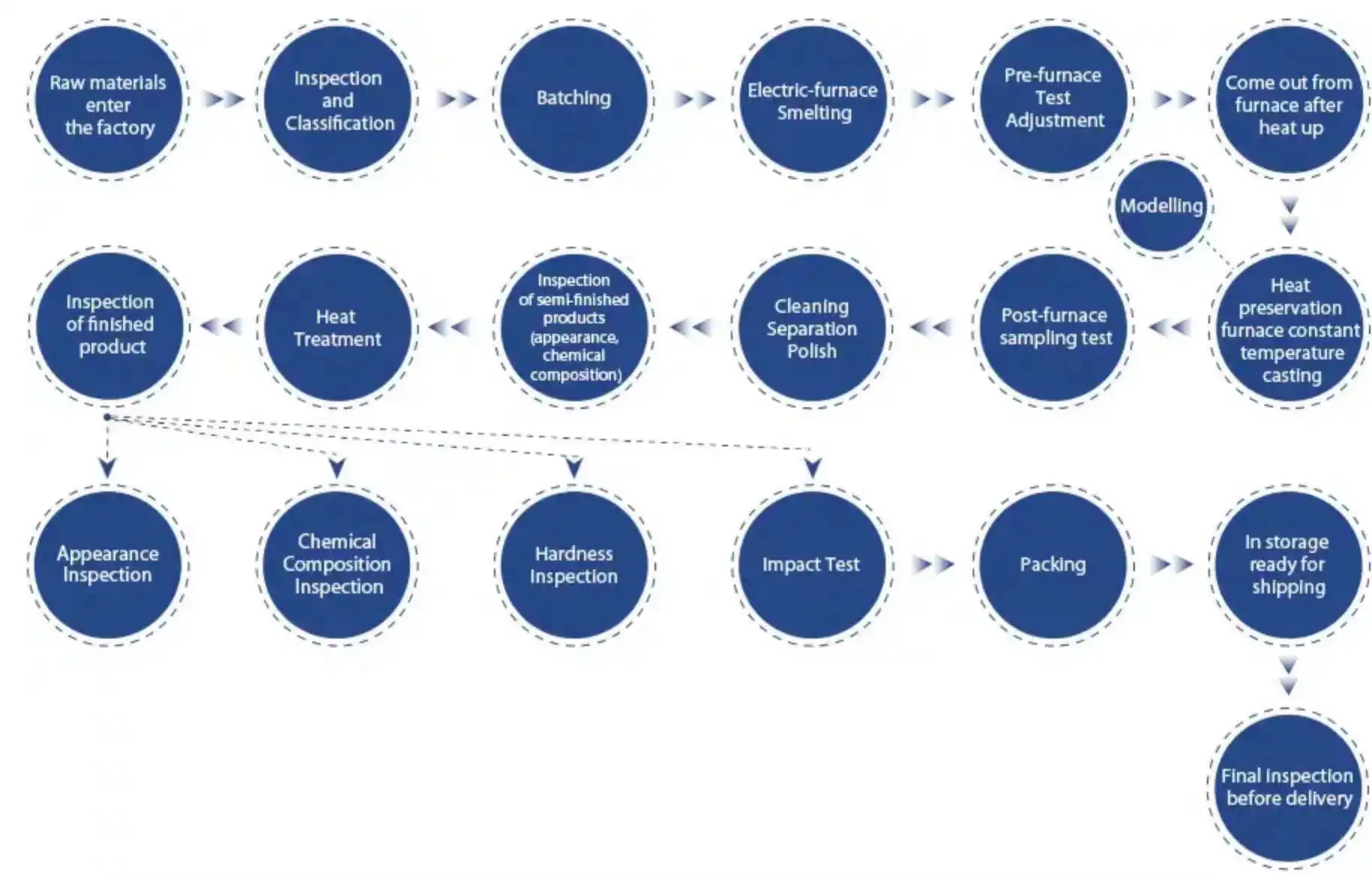
In the world of industrial grinding, high chrome grinding balls play a crucial role in enhancing efficiency and durability. These robust spheres are essential components in various industries, including cement production, mining, and power generation. But have you ever wondered about the intricate process behind their creation? Let's delve into the fascinating world of high chrome grinding ball production and uncover the secrets behind their exceptional performance.
What factors influence the quality of casting grinding balls?

In the world of industrial grinding, casting grinding balls play a crucial role in various sectors, including cement production, mining, and power generation. These spherical metallic tools are essential for breaking down materials into fine particles, and their quality can significantly impact the efficiency and effectiveness of grinding operations. Understanding the factors that influence the quality of casting grinding balls is vital for manufacturers and end-users alike. Let's delve into the key elements that determine the performance and durability of these indispensable grinding media.
The Ultimate Guide to Milling Balls
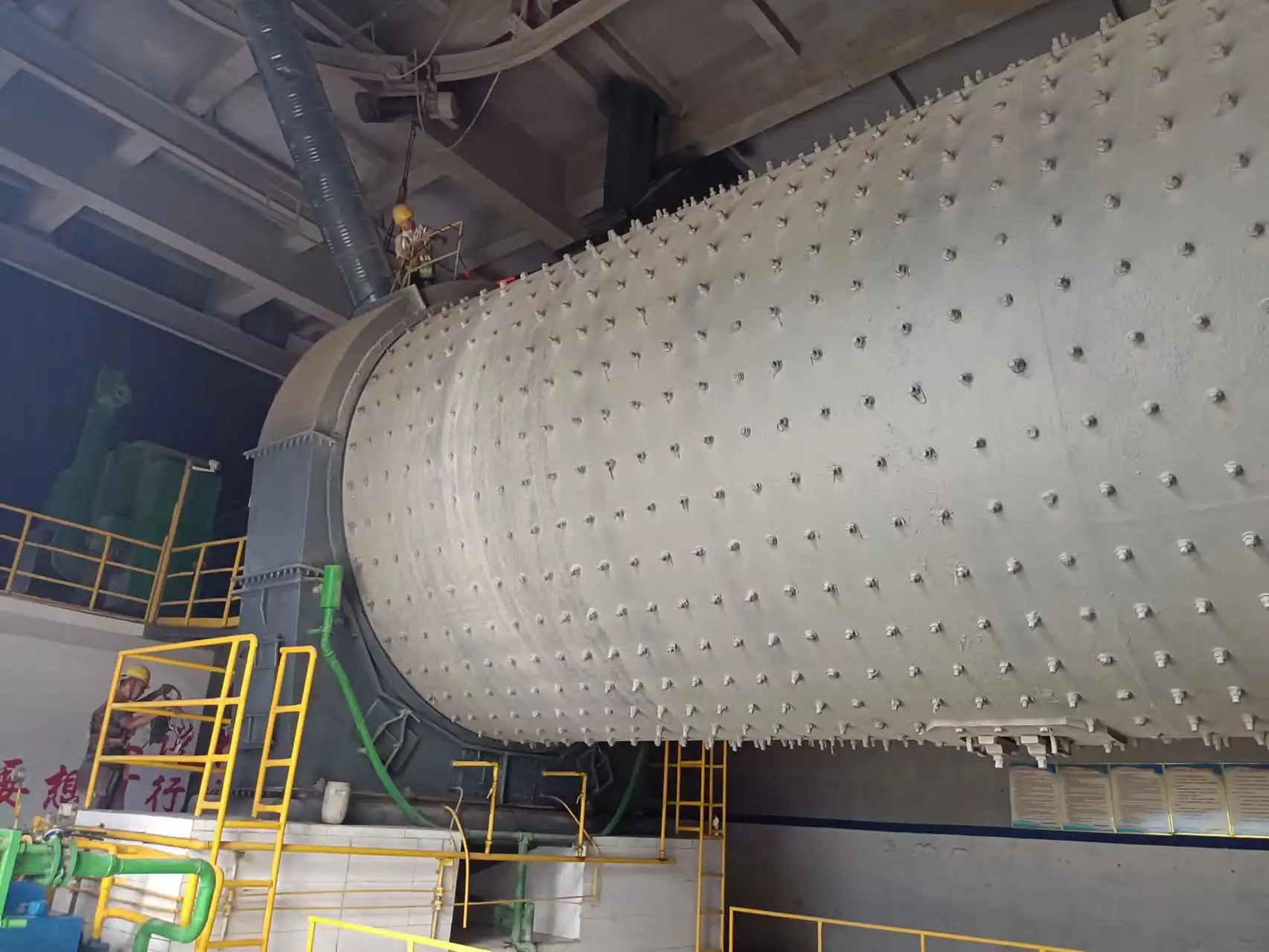
In the world of industrial grinding and material processing, milling balls play a crucial role in achieving optimal results. These small but mighty spheres are the unsung heroes of numerous industries, from mining to pharmaceuticals. This comprehensive guide will delve into the intricacies of milling balls, their applications, and how to choose the right ones for your specific needs.
What innovations are being made in grinding ball technology for mining?
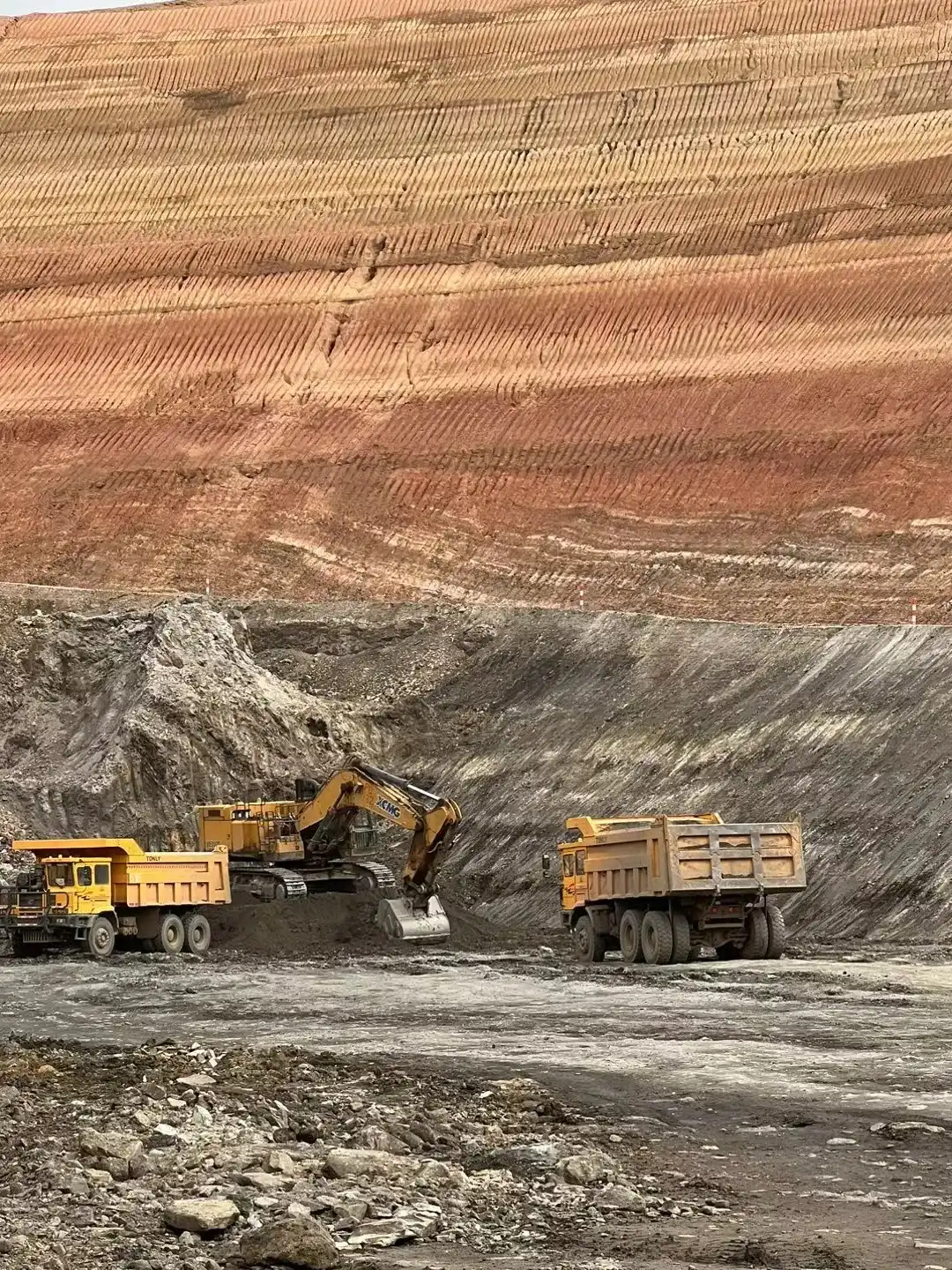
Grinding balls for mining have undergone significant technological advancements in recent years, revolutionizing the mineral processing industry. These innovations aim to enhance efficiency, durability, and performance while reducing operational costs. Some of the key developments include the introduction of high-chromium alloys, which offer superior wear resistance and longer service life. Additionally, manufacturers are experimenting with novel shapes and sizes, such as oval or cylindrical grinding media, to optimize grinding efficiency. Advanced manufacturing techniques, like powder metallurgy and precision casting, are being employed to produce grinding balls with improved microstructure and consistent quality. Moreover, smart coating technologies are being developed to further enhance the wear resistance and reduce contamination in the grinding process. These innovations collectively contribute to increased productivity, reduced energy consumption, and improved overall performance in mining operations.
What are high chrome steel grinding media balls?
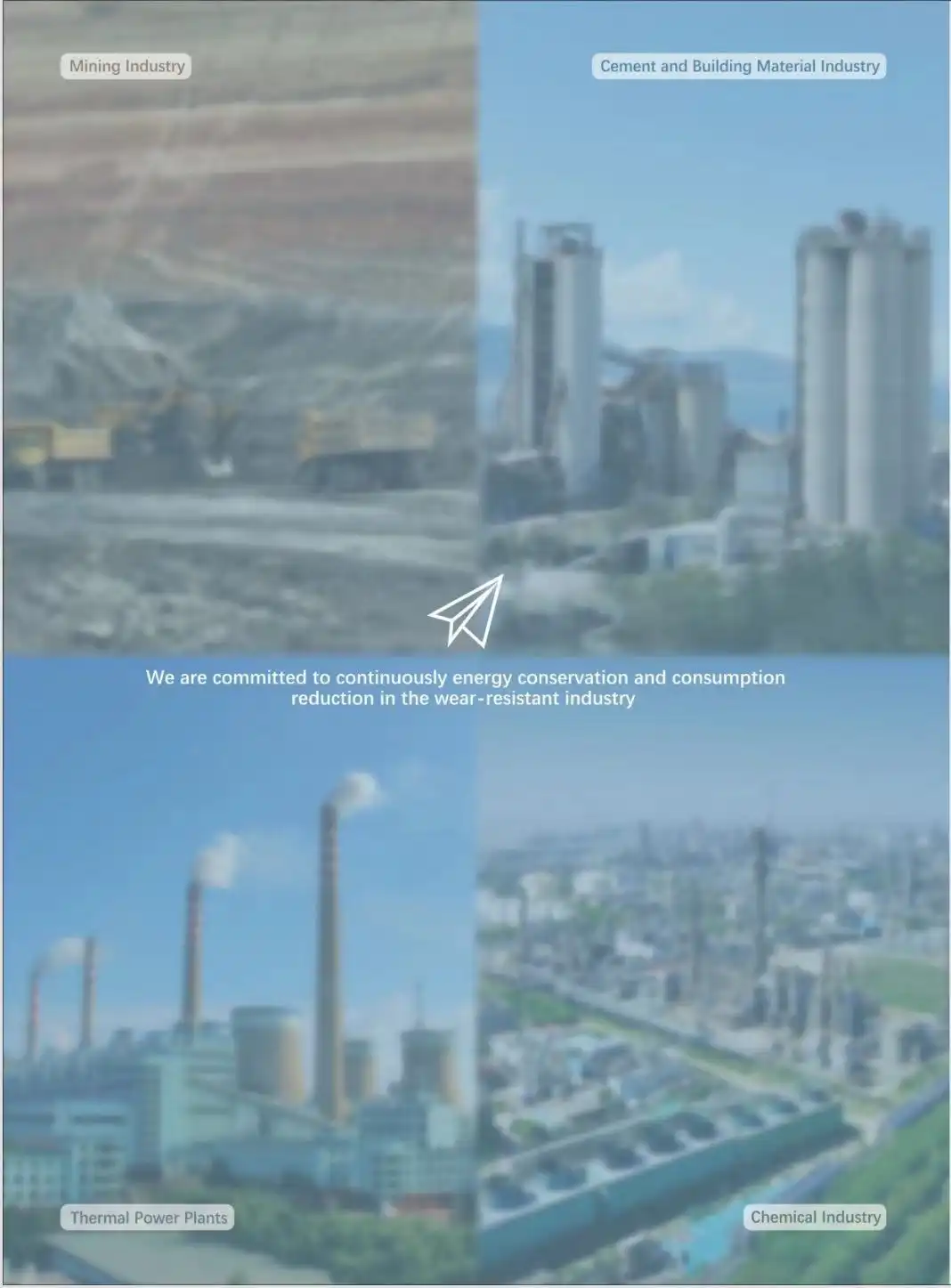
High chrome steel grinding media balls are essential components in various industrial processes, particularly in the mining, cement, and power generation sectors. These specialized balls are designed to withstand extreme wear and tear while efficiently grinding materials into fine particles. In this comprehensive guide, we'll explore the characteristics, applications, and benefits of high chrome steel grinding media balls, shedding light on their crucial role in modern industrial operations.
High chrome grinding media balls: A Comprehensive Guide
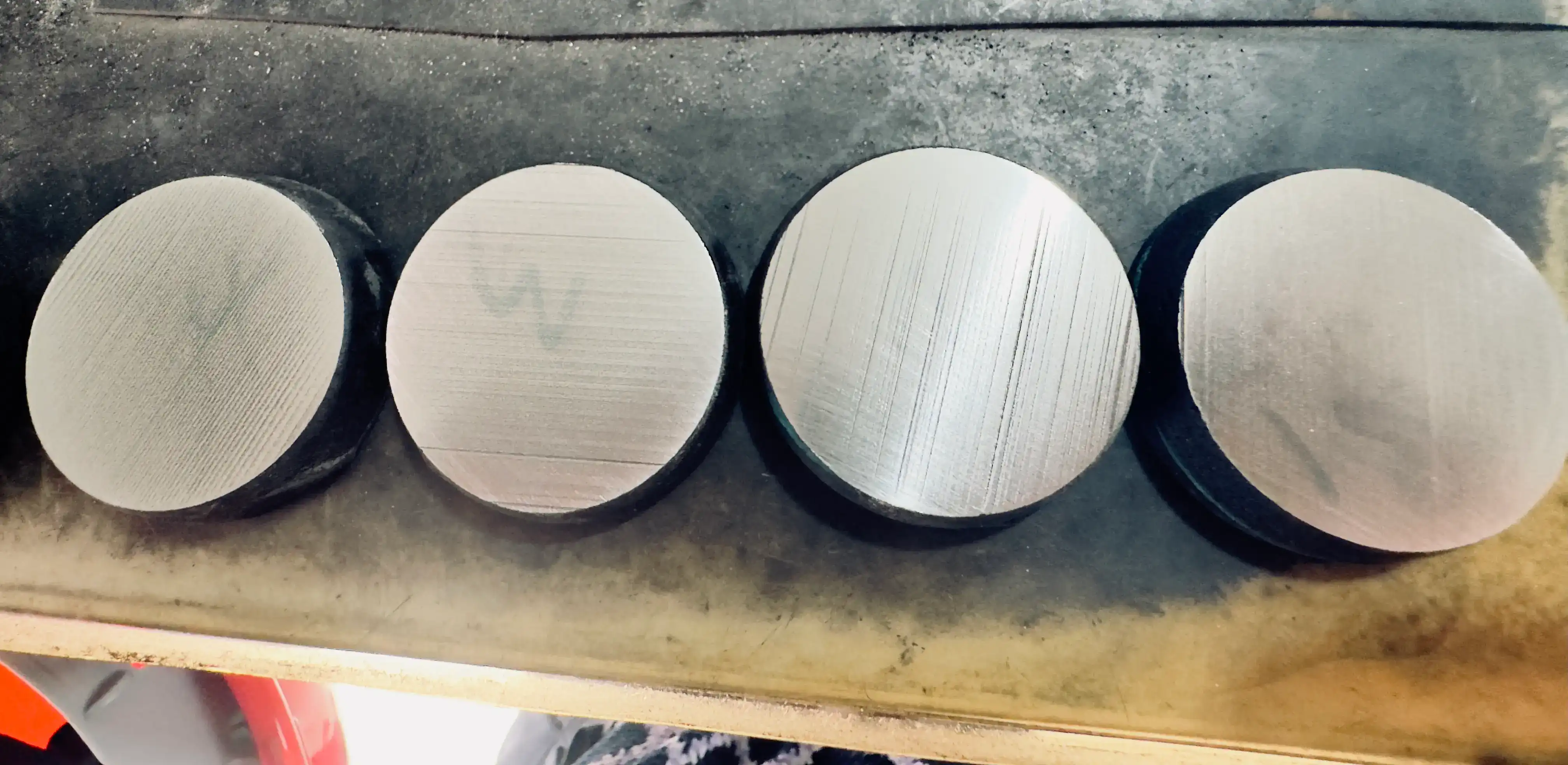
In the world of mineral processing, grinding media balls play a crucial role in reducing the size of materials and liberating valuable minerals. This comprehensive guide will delve into the intricacies of high chrome grinding media balls, exploring their functions, materials, and benefits in mineral processing operations. Whether you're in the mining, cement, or chemical industry, understanding the importance of high-quality grinding media is essential for optimizing your operations.
What are the economic implications of ball mill media wear rate?
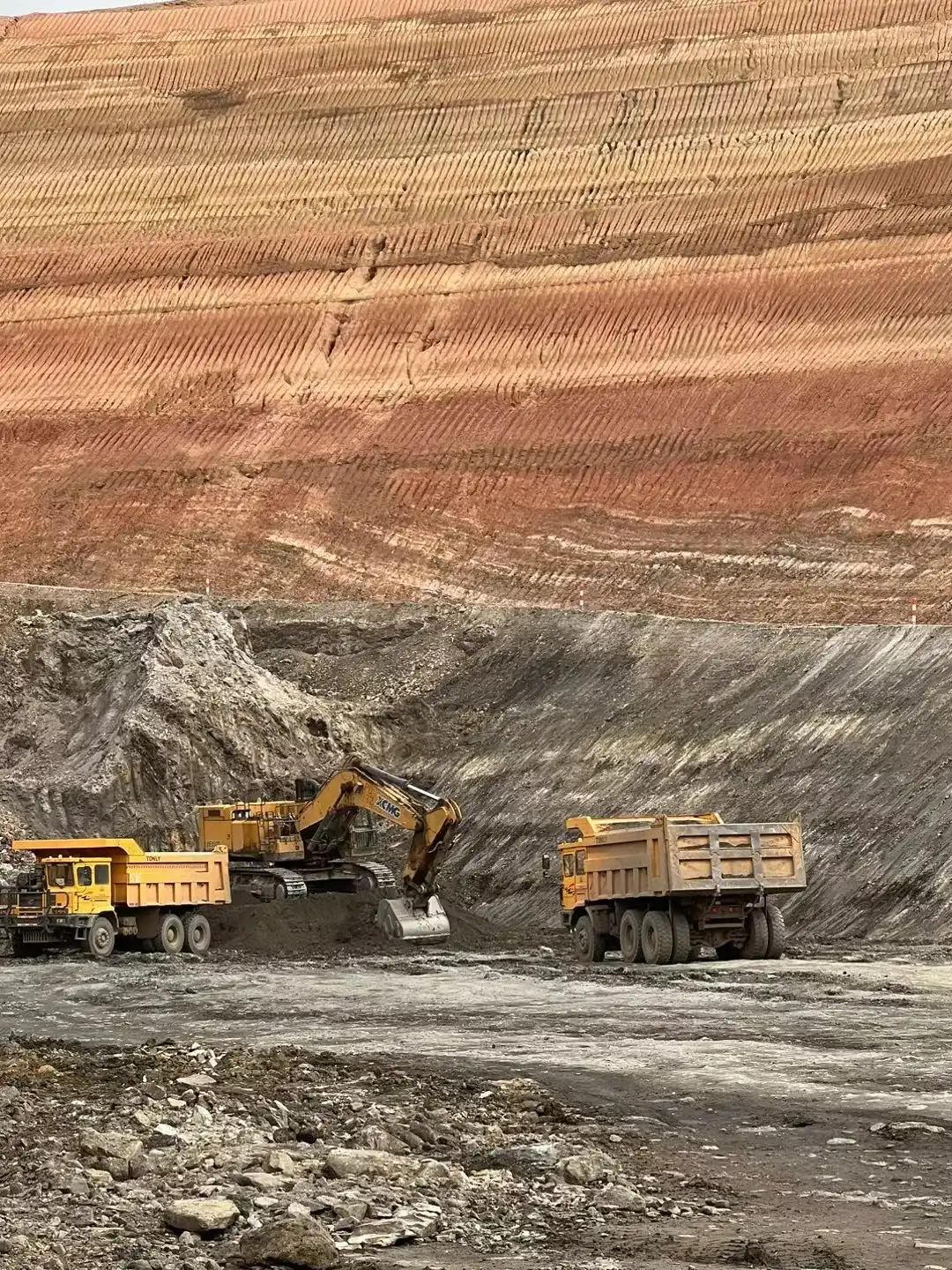
In the world of industrial grinding, the wear rate of ball mill media plays a crucial role in determining operational efficiency and cost-effectiveness. As a leading manufacturer of high-quality grinding media, NINGHU understands the significance of this factor in the overall economic landscape of various industries. This article delves into the economic implications of ball mill media wear rate, exploring how it affects total cost of ownership, long-term value, and return on investment.
What forces act on ball mill grinding media during rotation?
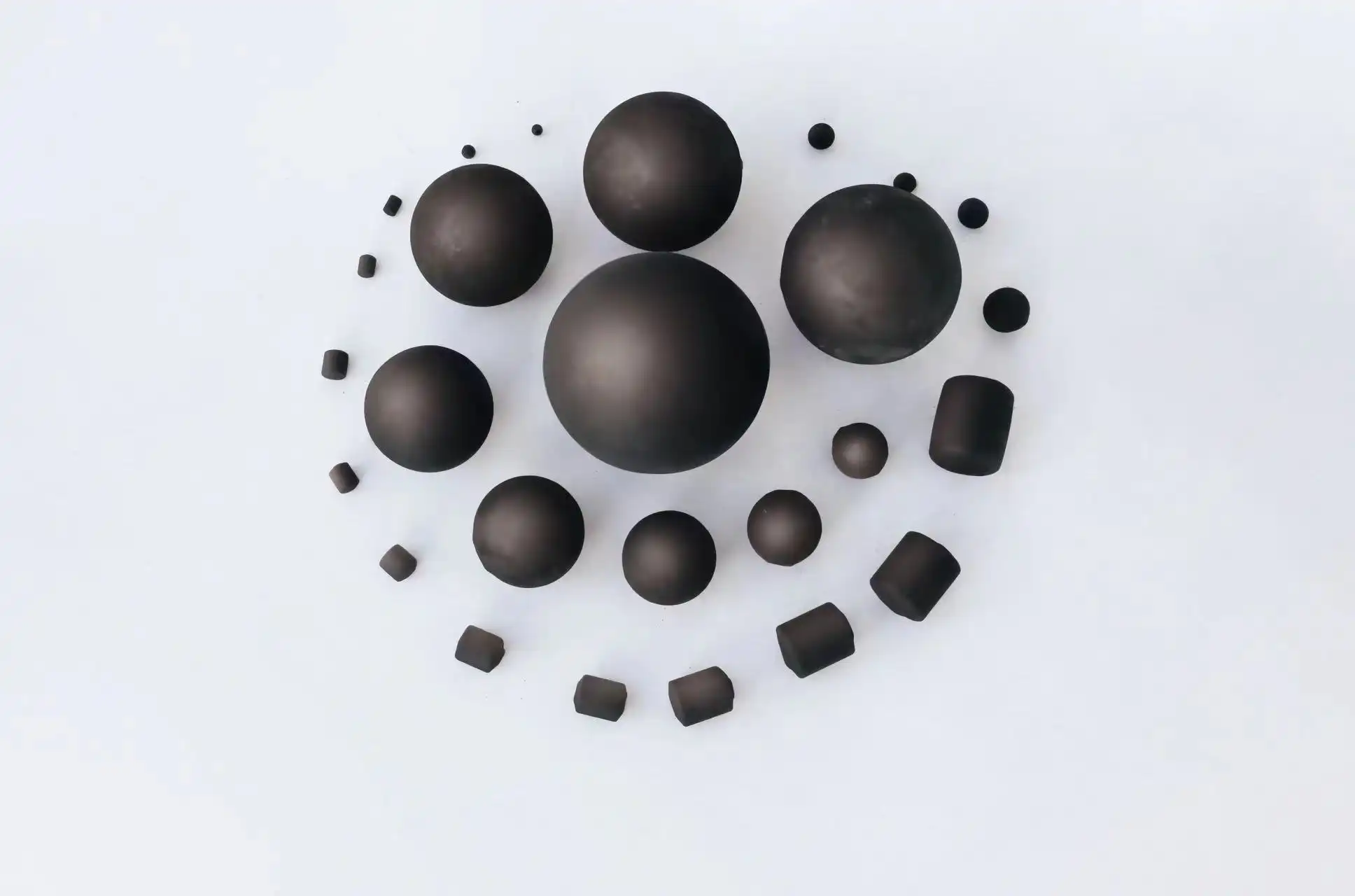
Ball mill grinding media play a crucial role in the comminution process, reducing particle sizes through a complex interplay of forces. Understanding these forces is essential for optimizing mill performance and achieving desired product characteristics. In this comprehensive guide, we'll explore the various forces acting on it during rotation, their effects on particle breakage, and how they contribute to the overall grinding efficiency.