Importance of Grinding Ball Density in Milling
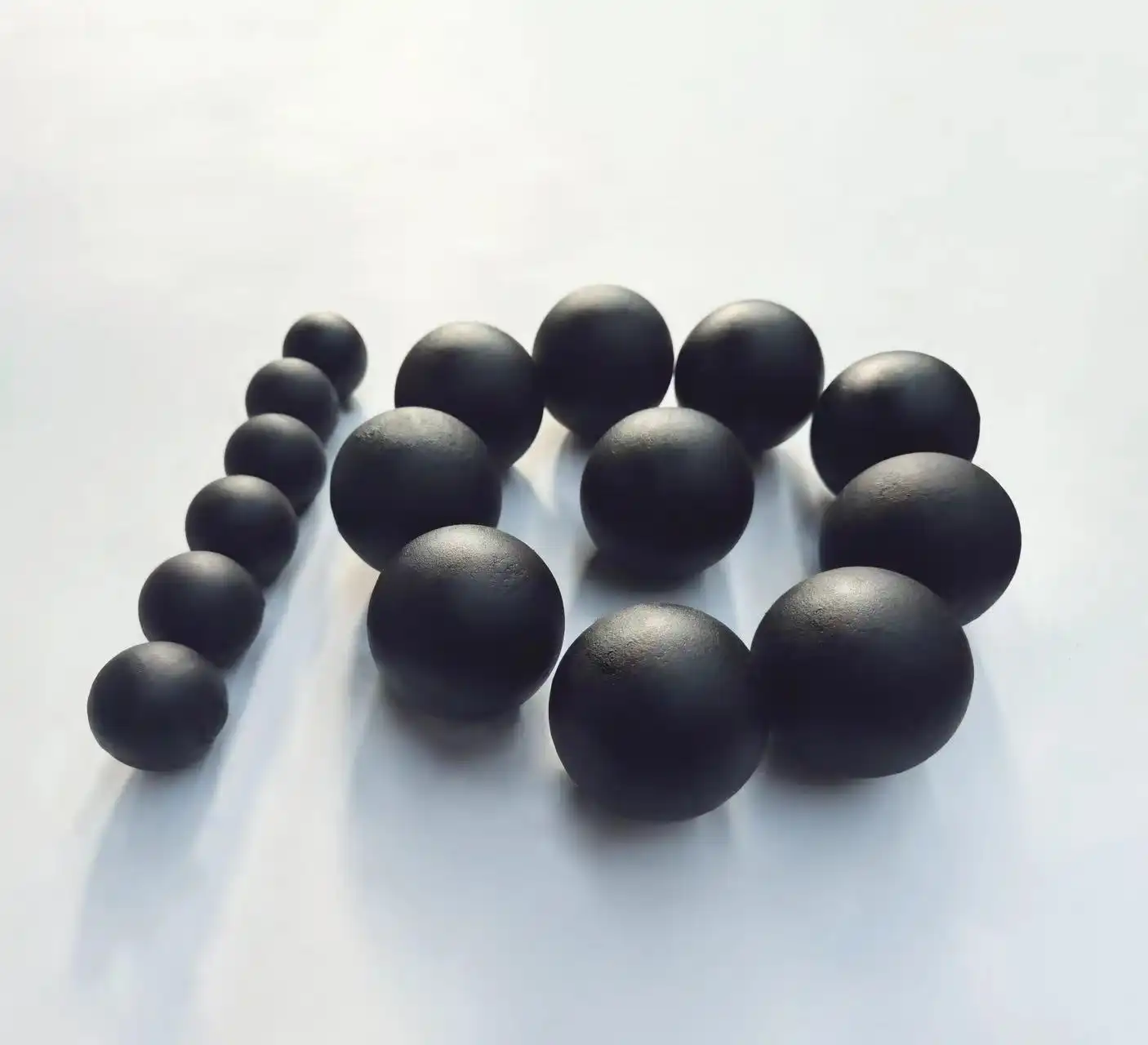
Crushing ball thickness plays a vital part in the proficiency of processing forms. It alludes to the mass of crushing media per unit volume. In less complex terms, it measures how thickly stuffed the crushing balls are inside the process. This thickness altogether influences the pounding proficiency, process throughput, and eventually, the quality of the last item. As such, understanding and controlling grinding balls thickness is fundamental for optimizing processing operations over different industries.
What is grinding media?
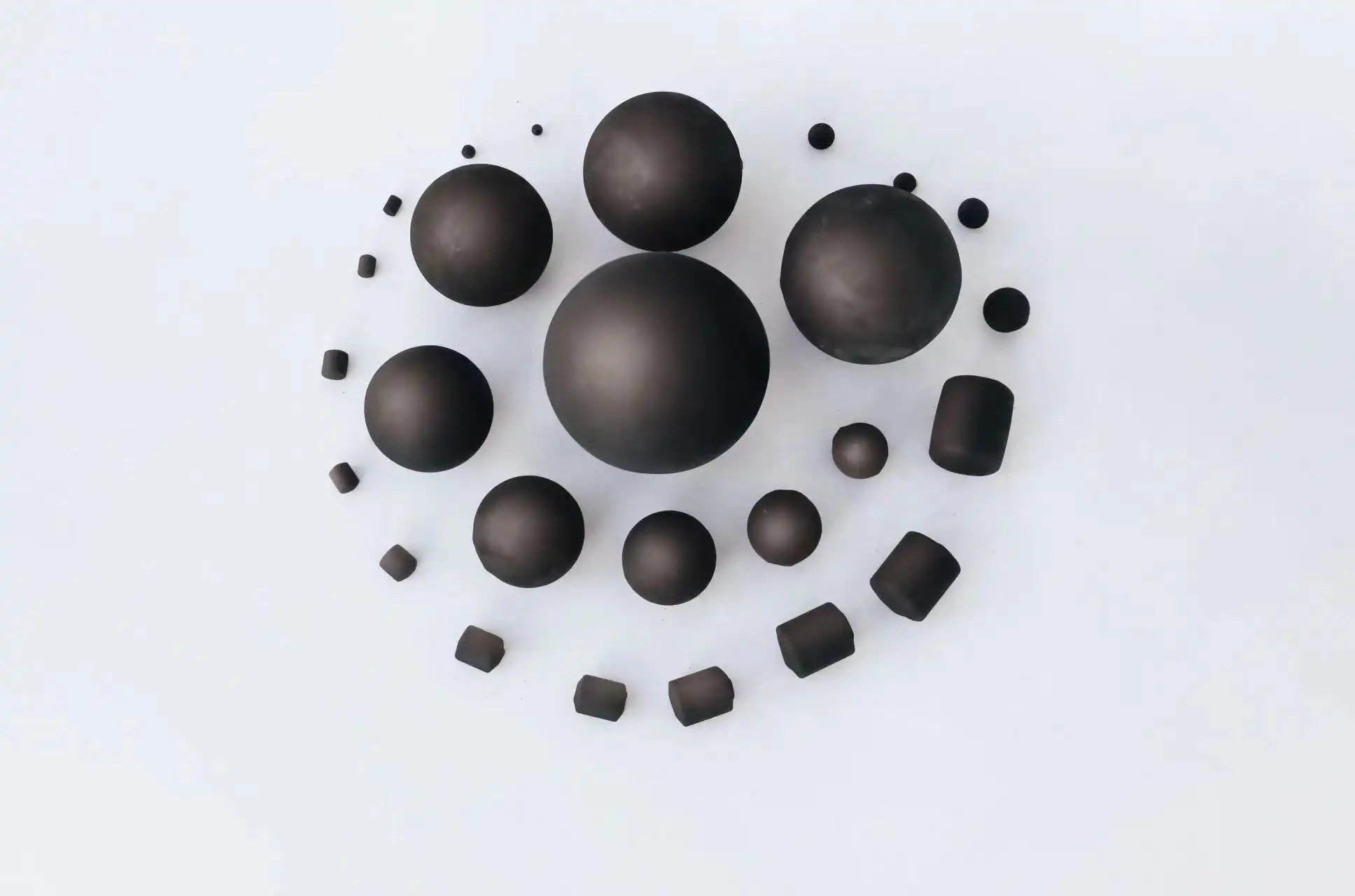
Grinding media are necessary parts of the process in mining, cement, and chemical industries. In order to make cement or extract valuable minerals more easily, they are used to break down materials into smaller pieces. For the devastating framework to be smoothed out, it is central to figure out the various sorts, impacts, and decision rules of devastating media.
What Role Do Grinding Balls Play in Ultra-Fine Grinding?
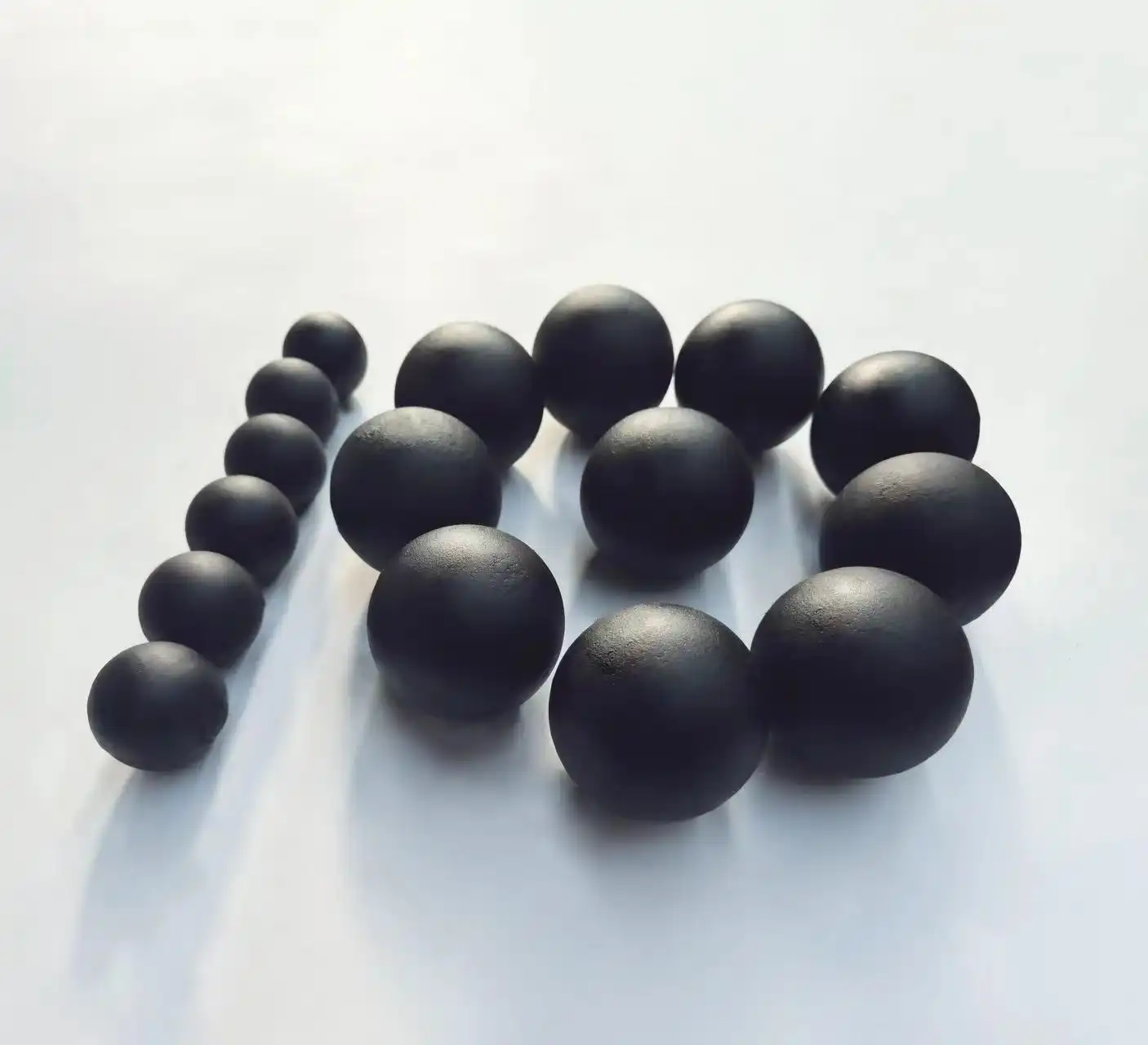
Grinding balls assume a significant part in the super fine grinding process, which is fundamental for creating fine particles and accomplishing wanted material properties in different ventures like mining, metallurgy, and drugs. These balls are produced using top notch materials like steel, earthenware production, or tungsten carbide, and are intended to endure the unforgiving states of the grinding system.
How to Improve Grinding Ball Efficiency?
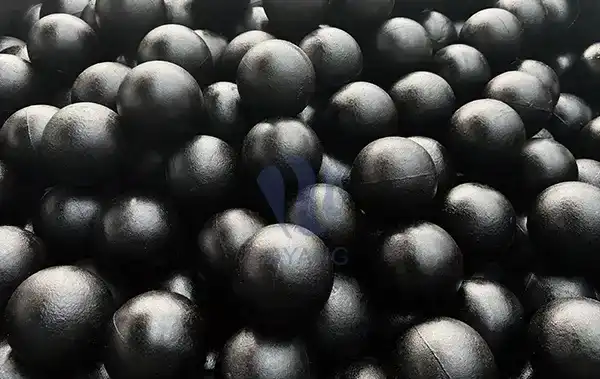
Grinding Ball are fundamental parts for mineral handling tasks, utilized in ball plants for finely crushing metal into particles. The production costs and overall milling performance are directly impacted by the efficiency of the grinding balls. In this blog, we discuss strategies and methods for increasing grinding ball efficiency, drawing on information from leading resources and expert advice.
How do you test the performance of grinding balls?
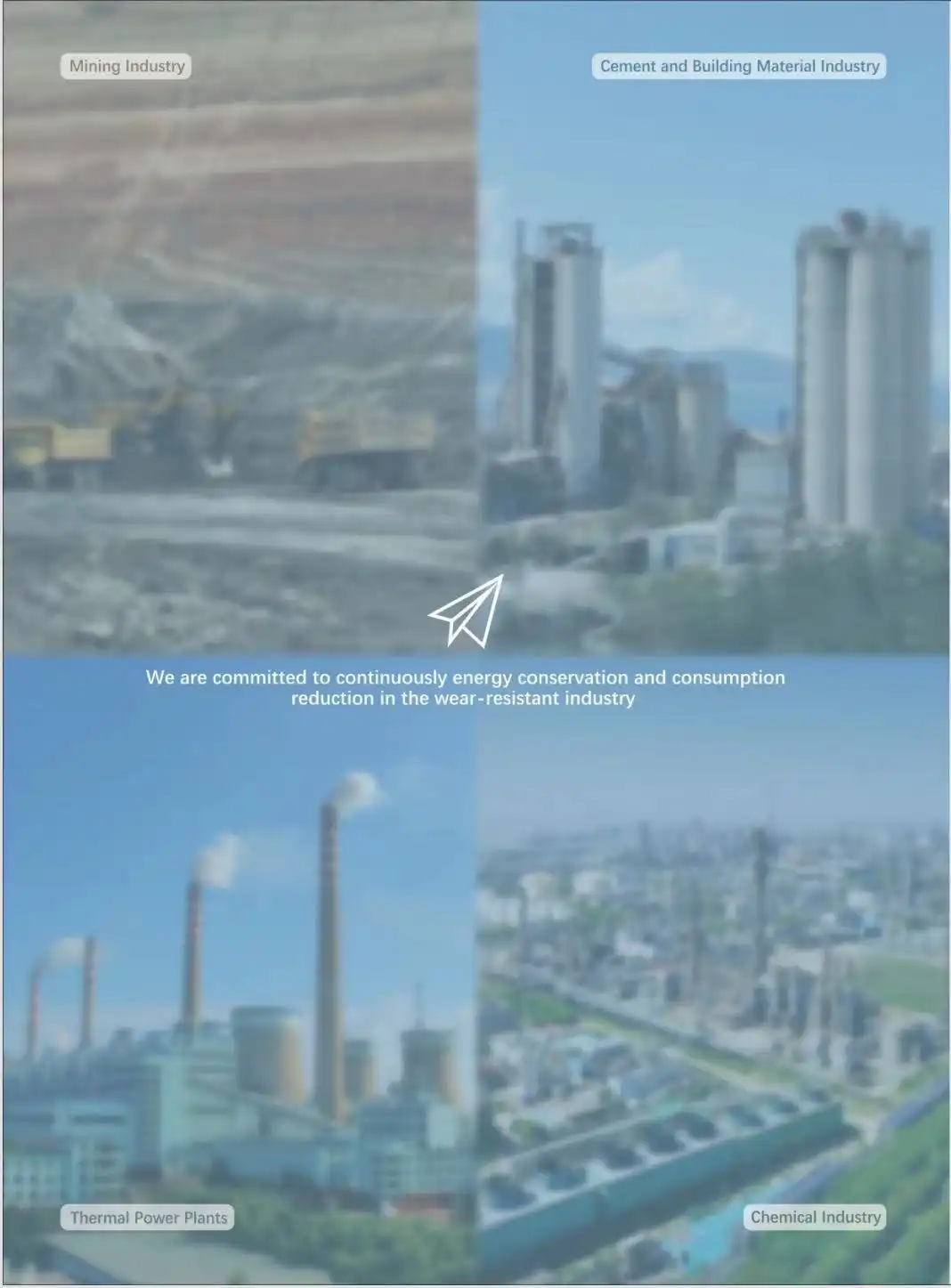
Grinding balls play a crucial role in various industrial processes where size reduction of raw materials is essential. Whether in mining, cement production, or any other sector requiring pulverization, the performance of grinding balls directly impacts efficiency and operational costs. Testing the performance of these balls is therefore critical to ensuring optimal grinding efficiency and cost-effectiveness in industrial operations.
How do high chrome grinding balls compare to low chrome grinding balls?
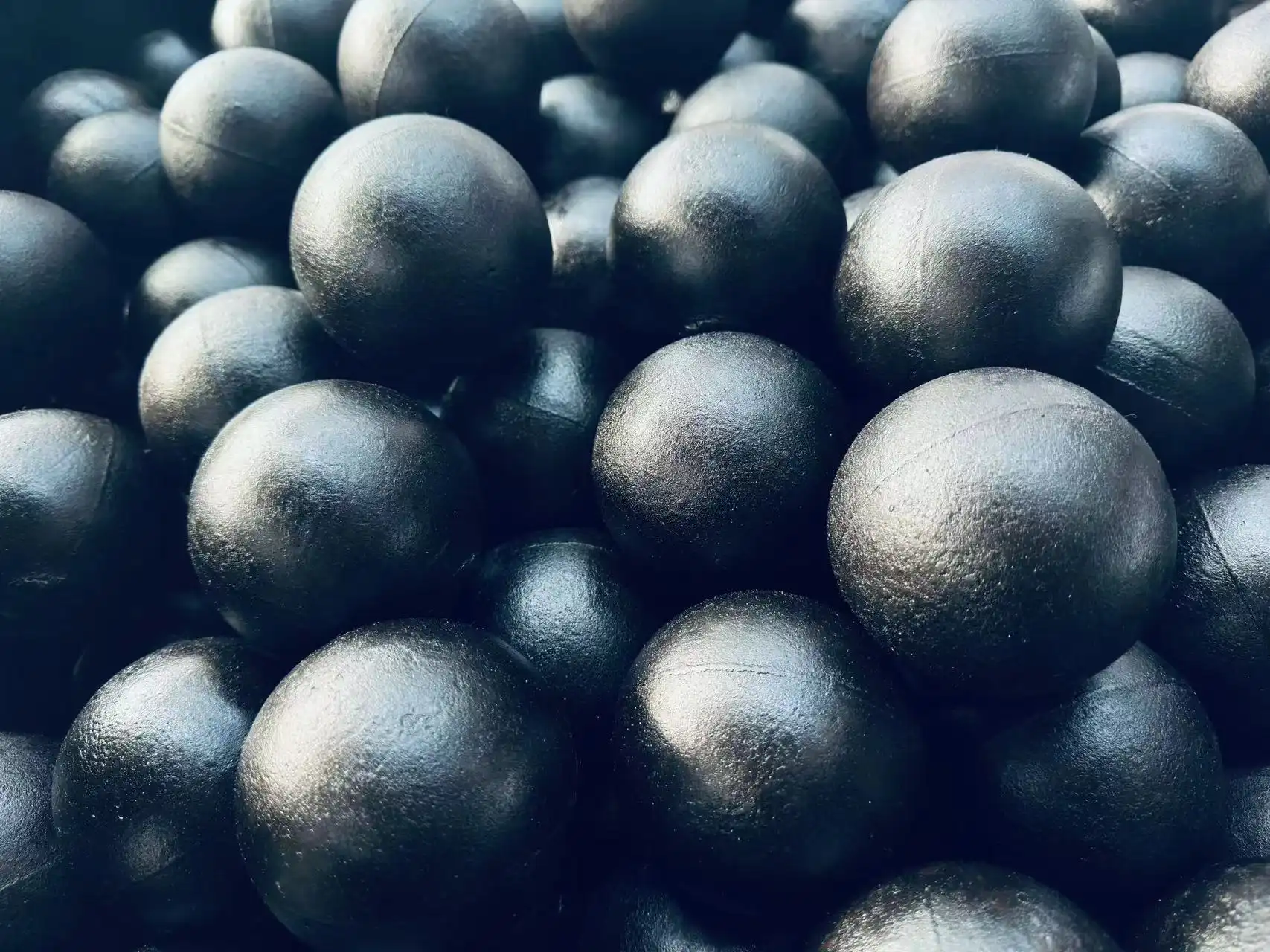
In the world of industrial grinding, the choice between high chrome and low chrome grinding balls can significantly impact the efficiency and cost-effectiveness of your operations. These essential components play a crucial role in various industries, including cement production, mining, and power generation. This comprehensive guide will delve into the key differences between high chrome grinding balls and their low chrome counterparts, helping you make an informed decision for your specific needs.
Can casting grinding balls be recycled or reused?
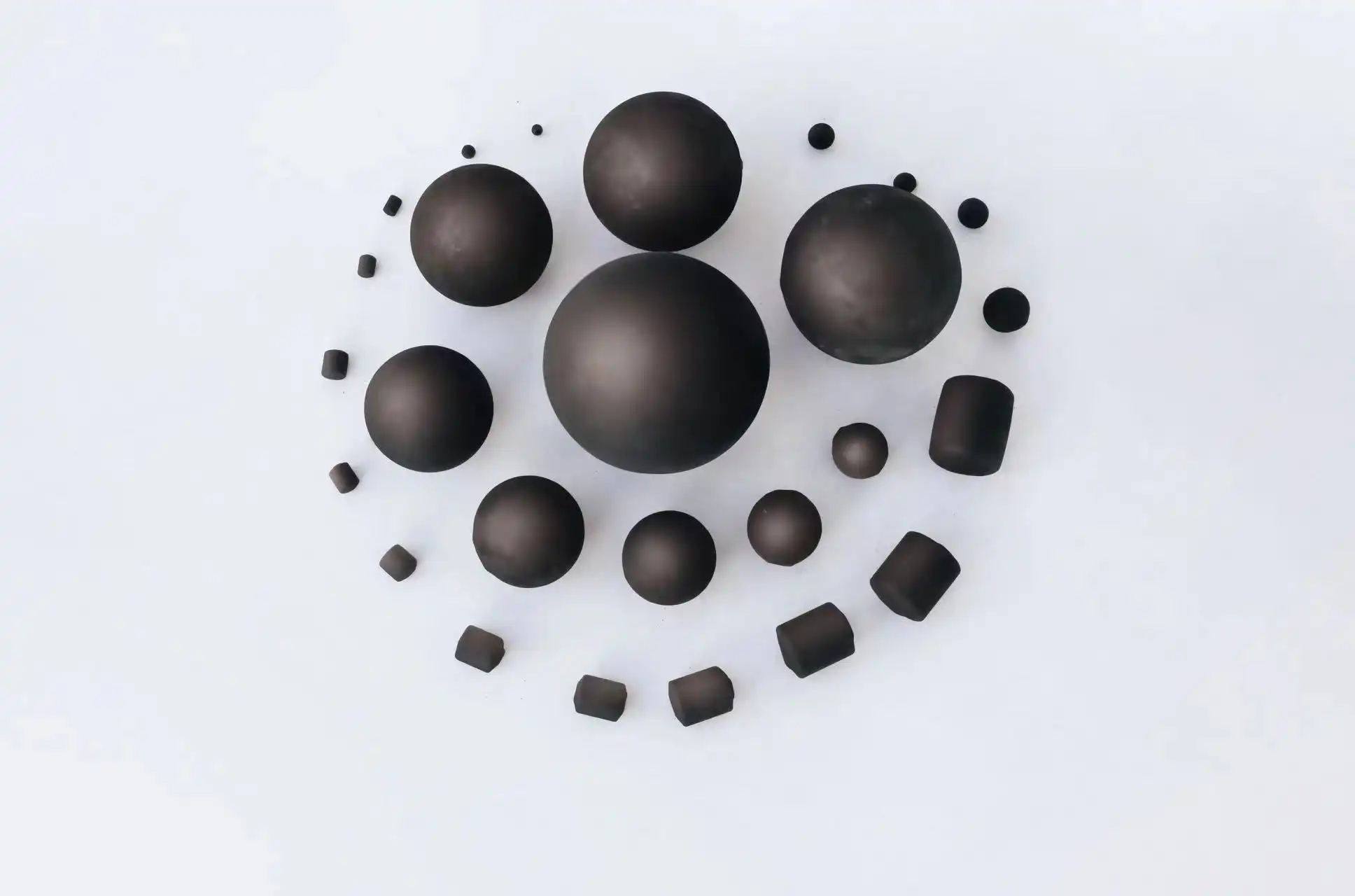
In the world of industrial grinding processes, casting grinding balls play a crucial role in reducing materials to fine particles. These hardwearing spheres are essential in industries such as cement production, mining, and power generation. However, as sustainability becomes increasingly important across all sectors, a pertinent question arises: Can casting grinding balls be recycled or reused? This article delves into the possibilities, challenges, and innovative approaches to extending the lifecycle of these indispensable industrial tools.
Milling Balls: Types and Applications
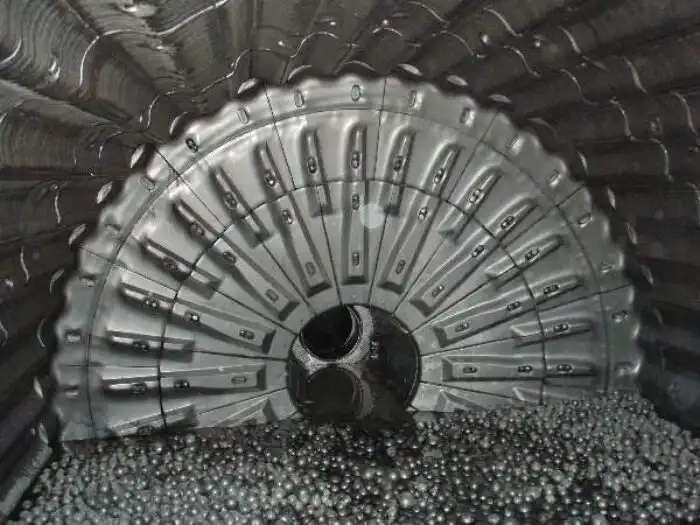
In the world of industrial processing, milling balls play a crucial role in grinding and refining materials across various sectors. These unassuming spheres are the workhorses of ball mills, tirelessly breaking down substances into finer particles. From the rugged terrains of mining operations to the pristine environments of pharmaceutical labs, milling balls are indispensable tools that shape the products we use daily. Let's dive into the fascinating world of these grinding powerhouses and explore their types, applications, and the latest innovations driving their evolution.
How high chrome grinding media balls Boosts Efficiency
Grinding Media Balls: Key to Mineral Processing Success
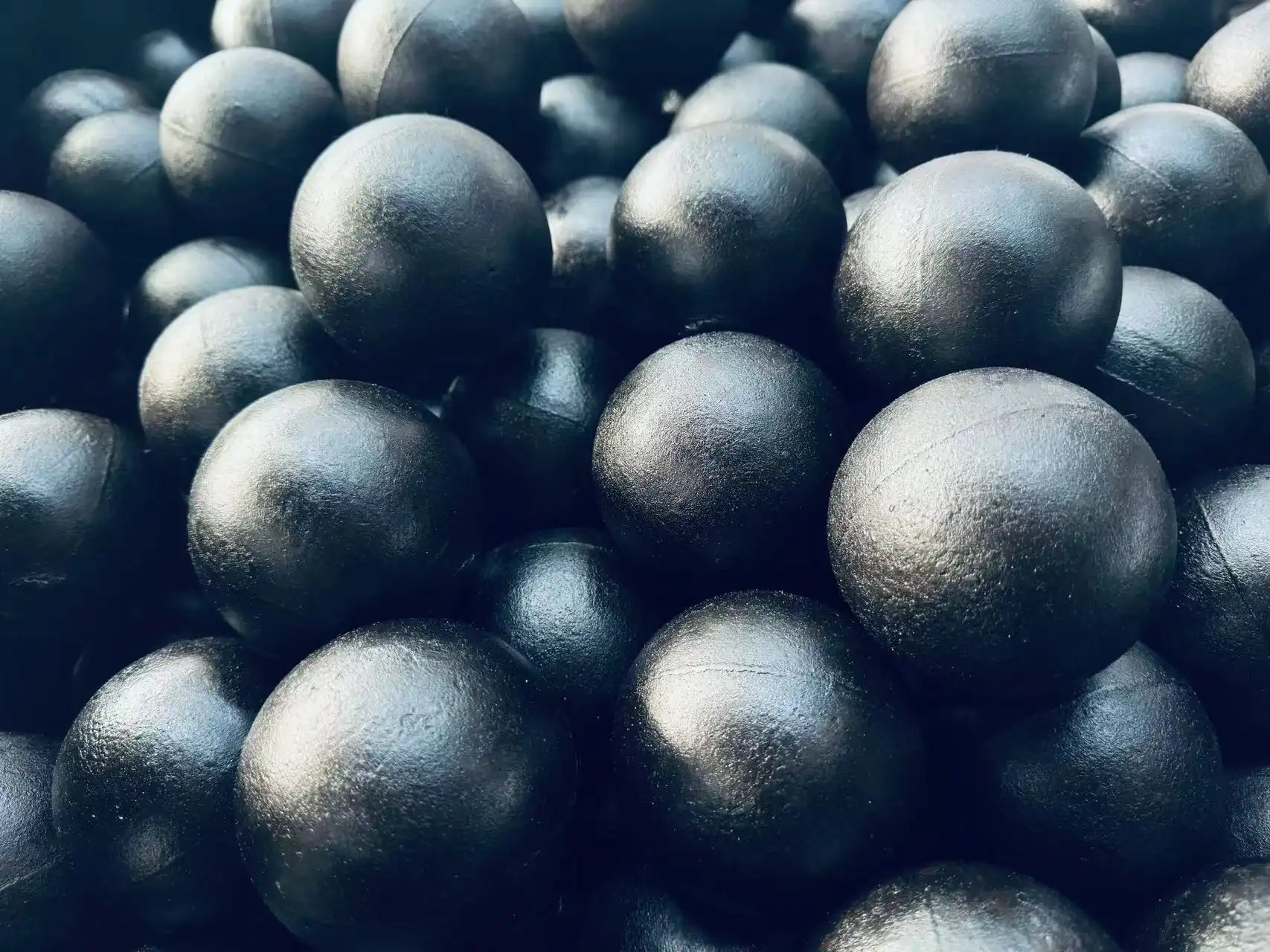
In the world of mineral processing, grinding media balls play a crucial role in achieving optimal results. These unassuming spheres are the workhorses of ball mills, pulverizing ore and other materials to extract valuable minerals. Understanding the intricacies of grinding media balls, like high chrome grinding media balls, can significantly impact the efficiency and effectiveness of your mineral processing operations.
How does mill shell design impact grinding media charge behavior?
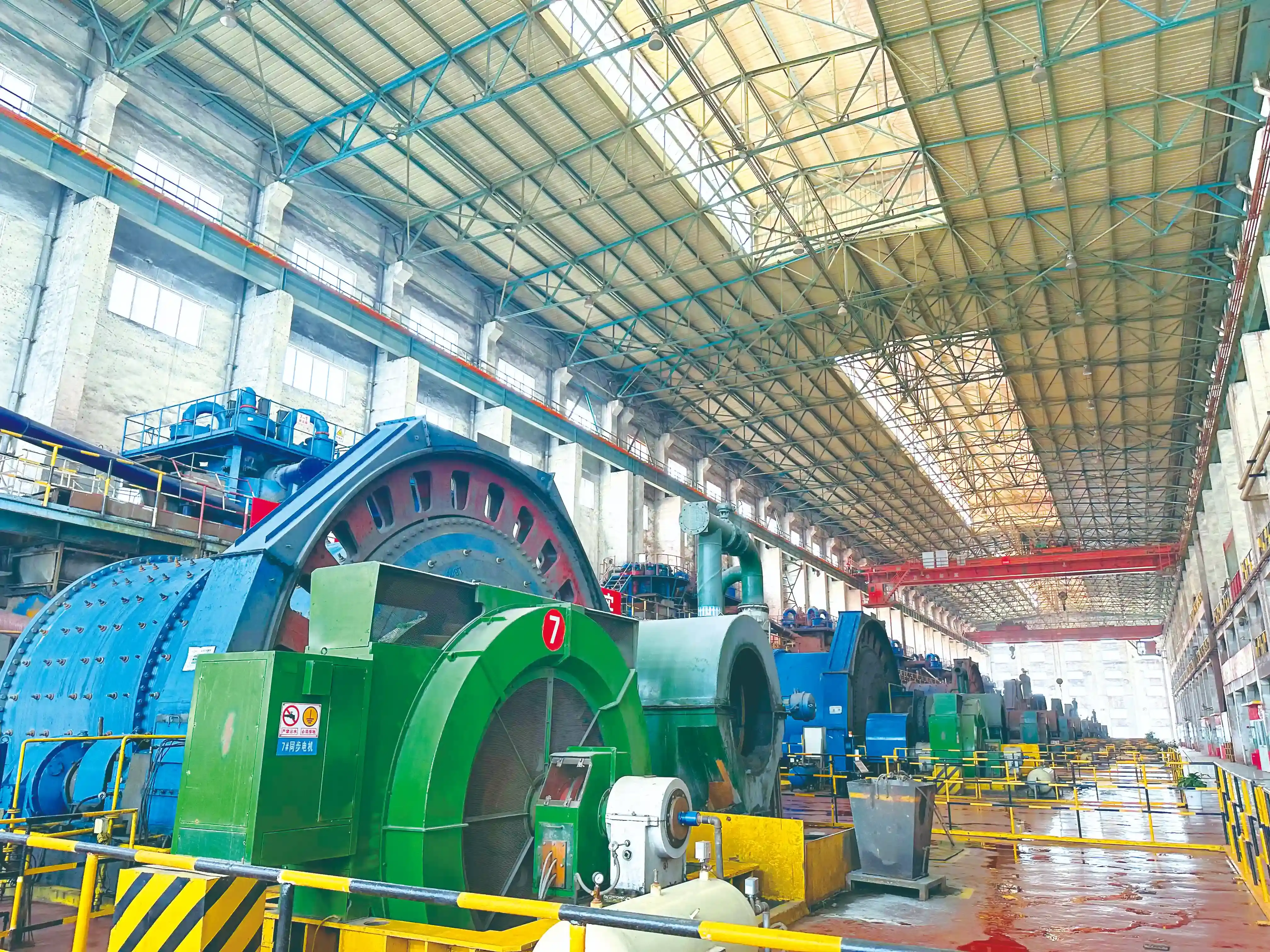
The design of a mill shell plays a crucial role in determining the behavior and efficiency of grinding media within ball mills. As a leading manufacturer of high-quality grinding media, NINGHU understands the importance of optimizing mill shell design to enhance the performance of ball mill grinding media. In this comprehensive guide, we'll explore how various aspects of mill shell design influence the motion and effectiveness of grinding media, ultimately impacting the overall grinding process.
How do high chrome steel grinding media balls improve grinding efficiency?
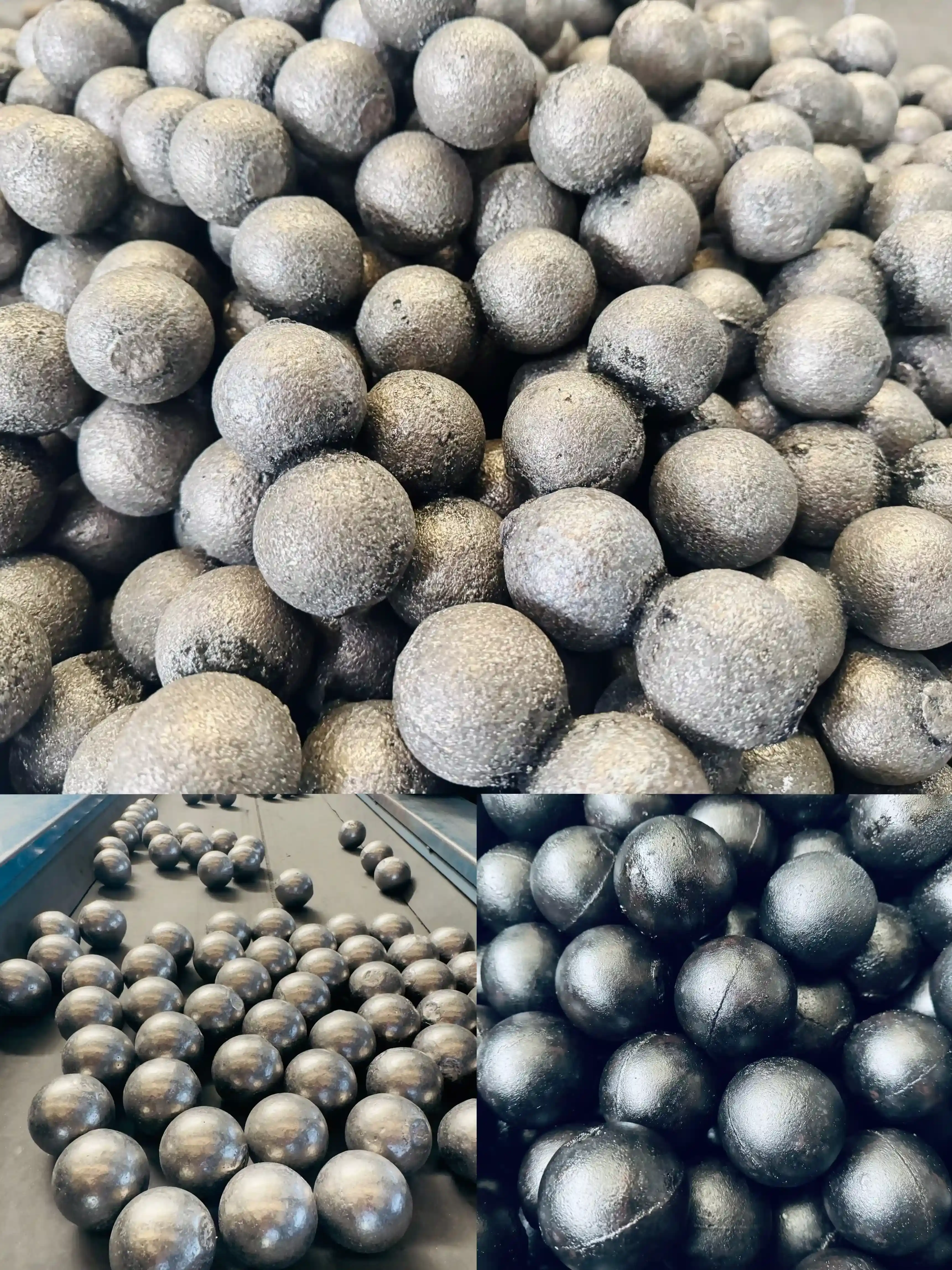
In the world of industrial grinding, efficiency is paramount. Companies are constantly seeking ways to enhance their grinding processes, reduce costs, and improve output quality. One significant advancement in this field has been the introduction of high chrome steel grinding media balls. These specialized grinding tools have revolutionized the industry, offering superior performance and longevity compared to their predecessors. Let's delve into how these innovative grinding media balls are transforming grinding efficiency across various sectors.