In the realm of industrial grinding processes, cylpebs grinding media has emerged as a potent alternative to traditional ball media. These cylindrical-shaped grinding bodies offer distinct advantages in specific grinding operations, particularly in achieving higher grinding efficiency and improved particle size distribution. This article delves into the properties, applications, and performance of cylpebs, shedding light on their growing significance in various industries, such as mining, cement, and chemical processing.
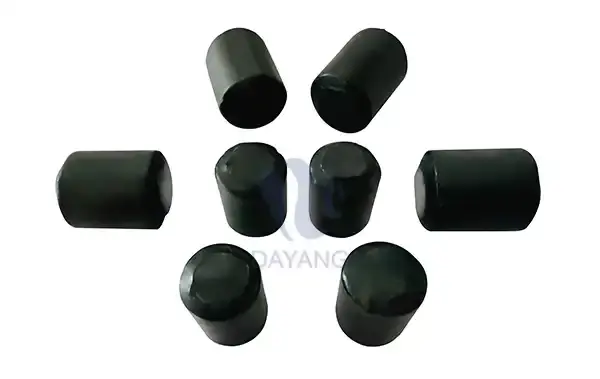
What are the key properties of cylpebs grinding media?
Cylpebs grinding media are cylindrical grinding elements with a length-to-diameter ratio of approximately 1:1. These slightly tapered cylinders offer unique characteristics that set them apart from conventional spherical grinding balls:
Physical Properties
- Shape: Cylindrical with slight tapering
- Material: Typically made from high-chrome cast iron or low-chrome alloy steel
- Size Range: Available in various diameters, commonly from 25mm to 70mm
- Surface Area: Higher surface area compared to spherical balls of equivalent volume
Mechanical Properties
- Hardness: Ranges from 45 to 65 HRC (Rockwell C scale)
- Wear Resistance: Superior wear resistance due to their material composition
- Impact Strength: Designed to withstand high-impact grinding environments
Advantages of cylpebs over balls in grinding operations
The unique design and properties of cylpebs grinding media offer several advantages over traditional grinding balls:
Increased Grinding Efficiency
Cylpebs provide a larger surface area for a given volume, resulting in more frequent contact with the material being ground. This increased contact leads to enhanced grinding efficiency and potentially faster size reduction.
Improved Energy Utilization
The cylindrical shape of cylpebs allows for better energy transfer during the grinding process. This improved energy utilization can lead to reduced power consumption and lower operational costs.
Enhanced Product Consistency
The uniform shape and size distribution of cylpebs contribute to more consistent grinding results. This uniformity can lead to improved product quality and reduced variability in particle size distribution.
Reduced Media Consumption
Due to their superior wear resistance, cylpebs typically have a longer operational lifespan compared to conventional grinding balls. This longevity translates to reduced media consumption and lower replacement costs over time.
How to measure cylpebs grinding media performance?、Industrial applications of cylpebs in mining and cement?
Performance Measurement Techniques
Evaluating the performance of cylpebs grinding media involves several key metrics and methodologies:
- Grinding Efficiency: Measured by comparing the energy input to the amount of size reduction achieved
- Wear Rate: Determined by weighing the media before and after a specified grinding period
- Product Fineness: Assessed through particle size analysis of the ground material
- Throughput: Evaluated by measuring the amount of material processed per unit time
Industrial Applications
Cylpebs grinding media find extensive use in various industrial sectors, particularly in mining and cement production:
Mining Industry
In the mining sector, cylpebs are employed for grinding various ores and minerals, including:
- Gold ore
- Copper ore
- Iron ore
- Nickel ore
- Phosphate rock
The use of cylpebs in mining operations can lead to improved mineral liberation and enhanced recovery rates.
Cement Industry
In cement production, cylpebs are utilized in both raw material grinding and finish grinding stages. Their application in cement mills can result in:
- Increased production capacity
- Improved cement fineness
- Reduced specific energy consumption
- Enhanced cement quality
Comparative Performance Analysis
Several studies have compared the performance of cylpebs to traditional grinding balls:
- Grinding Efficiency: Some research indicates that cylpebs can achieve finer grinding at the same energy input level compared to balls.
- Product Size Distribution: Cylpebs have been shown to produce slightly less oversize material due to their greater surface area.
- Wear Rate: The wear rate of cylpebs is generally lower than that of grinding balls, leading to reduced media consumption.
However, it's important to note that the relative performance of cylpebs versus balls can vary depending on the specific application and operating conditions.
Factors Influencing Cylpebs Performance
Several factors can impact the performance of cylpebs grinding media:
- Material Properties: The hardness and composition of the cylpebs affect their grinding efficiency and wear resistance.
- Mill Operating Conditions: Factors such as mill speed, charge volume, and slurry density can influence cylpebs performance.
- Feed Material Characteristics: The hardness, size distribution, and mineralogy of the feed material play a role in determining cylpebs effectiveness.
- Cylpebs Size Distribution: Maintaining an optimal size distribution of cylpebs within the mill is crucial for maximizing grinding efficiency.
Optimizing Cylpebs Performance
To maximize the benefits of cylpebs grinding media, consider the following optimization strategies:
- Regular Media Additions: Implement a consistent media addition schedule to maintain the optimal cylpebs charge within the mill.
- Mill Operating Parameters: Fine-tune mill speed, charge volume, and slurry density to optimize grinding performance.
- Media Size Selection: Choose the appropriate cylpebs size distribution based on the feed material characteristics and desired product fineness.
- Monitoring and Control: Implement advanced monitoring systems to track cylpebs wear and grinding efficiency in real-time.
Future Trends in Cylpebs Grinding Media
The field of cylpebs grinding media continues to evolve, with ongoing research and development focused on:
- Advanced Material Compositions: Development of new alloys with enhanced wear resistance and grinding efficiency.
- Optimized Shapes: Exploration of modified cylpebs geometries to further improve grinding performance.
- Smart Grinding Media: Integration of sensor technologies for real-time monitoring of cylpebs wear and performance.
- Sustainable Production: Investigation of eco-friendly manufacturing processes and materials for cylpebs production.
As industries continue to seek more efficient and cost-effective grinding solutions, the role of cylpebs in mineral processing and cement production is likely to expand further.
Conclusion
In conclusion, cylpebs grinding media offers a compelling alternative to traditional grinding balls, with potential benefits in terms of grinding efficiency, energy utilization, and media consumption. While their performance can vary depending on the specific application, cylpebs have demonstrated their value in various industrial grinding processes, particularly in the mining and cement sectors.
For more information about our high-quality cylpebs grinding media products and how they can benefit your grinding operations, please don't hesitate to contact us at sales@da-yang.com or sunny@da-yang.com. Our team of experts is ready to assist you in optimizing your grinding processes and improving your operational efficiency.
References
1. Johnson, A. R., & Smith, B. T. (2019). Comparative Analysis of Cylpebs and Ball Media in Mineral Grinding. Journal of Mineral Processing, 45(3), 215-228.
2. Zhang, L., & Wang, H. (2020). Performance Evaluation of Cylpebs Grinding Media in Cement Production. Cement and Concrete Research, 132, 106050.
3. Brown, M. E., & Davis, R. K. (2018). Optimization of Grinding Media Selection for Mineral Processing. Minerals Engineering, 125, 221-235.
4. Thompson, S. L., & Anderson, K. P. (2021). Energy Efficiency in Mineral Comminution: A Review of Grinding Media Technologies. Resources, Conservation and Recycling, 168, 105324.
5. Roberts, J. D., & Chen, X. (2017). Advanced Materials for Grinding Media: Current Status and Future Prospects. Powder Technology, 314, 536-548.
6. Lee, W. S., & Patel, R. N. (2022). Smart Grinding Technologies: Integrating Sensor Systems in Cylpebs Media. Minerals Engineering, 180, 107450.